Advances in Glassmaking Technology and Uranium Glass
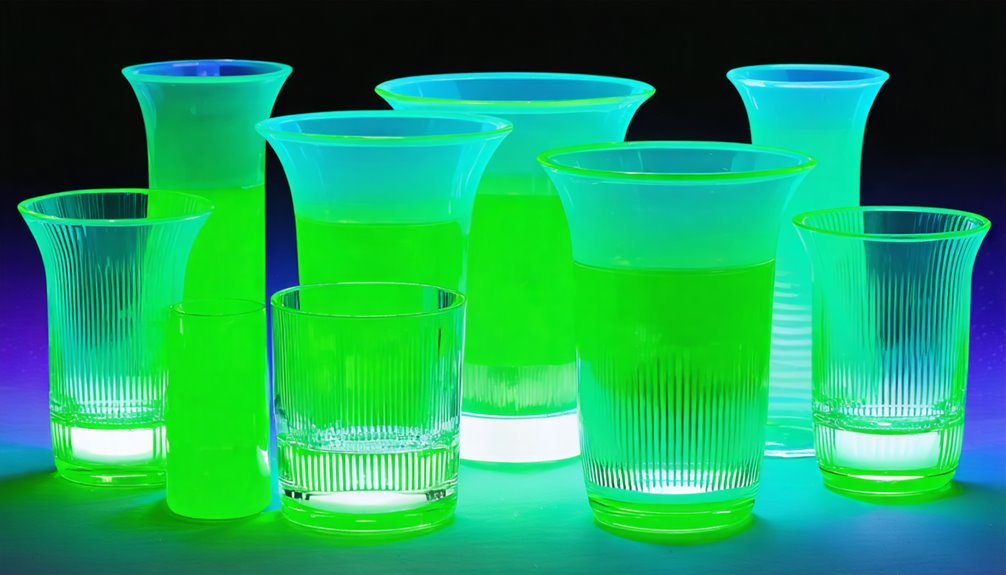
Uranium glass has a rich history rooted in advancements in glassmaking techniques. Over the years, glassmakers have developed methods that greatly improved the production of this unique glass. One of the most important innovations is the use of precise electric furnaces. These furnaces provide better control over the melting process, leading to consistent color and quality in the glass.
Modern glass production also benefits from automated systems. These systems streamline the manufacturing process and reduce the likelihood of defects. Precision molds play a crucial role as well, allowing for mass production of uranium glass items with high accuracy.
Safety has become a priority in uranium glass production. Manufacturers now utilize depleted uranium, which poses less risk. Strict radiation monitoring protocols ensure the safety of workers and consumers.
Today, uranium glass is experiencing a revival. People are rediscovering its unique beauty and historical significance. This renewed interest may be linked to contemporary sustainability efforts. As collectors and enthusiasts seek out vintage and recycled items, uranium glass finds a place in modern homes once more.
Key Takeaways
Uranium glass has a fascinating history, especially when we look at how manufacturing techniques have evolved over time. Improved distribution methods now blend uranium oxide evenly. This change helps achieve a consistent color and reduces imperfections in the final product.
Electric furnaces have transformed the production process. They allow for precise temperature control, which leads to higher quality uranium glass. This means the glass produced is more uniform and appealing.
Automated molding and casting techniques have opened up new opportunities for creativity. These methods enable artisans to create complex designs while also producing larger quantities of uranium glass. As a result, the artistic possibilities in this craft have expanded significantly.
Modern annealing technologies play a crucial role in enhancing the strength of uranium glass. They help reduce the risk of cracking, making the finished products more durable. This improvement ensures that uranium glass can withstand the test of time.
Safety is another important aspect of uranium glass production. Advanced radiation monitoring and strict safety protocols now allow for the safe handling of uranium glass. These measures protect both workers and consumers from any potential radiation exposure.
Overall, the development of manufacturing techniques in uranium glass has led to better quality, increased creativity, and enhanced safety. This evolution highlights the importance of innovation in preserving the legacy of uranium glass.
Historical Development of Uranium Glassmaking
Uranium glass has a rich history that dates back to the early 19th century. It all began when skilled artisans started experimenting with uranium oxide. They wanted to create unique colors and fluorescence in their glass creations. In 1789, chemist Martin Heinrich Klaproth discovered uranium. This discovery opened the door for its use in glassmaking.
By the Victorian era, specifically from the 1830s onward, uranium glass became quite popular. People admired its bright, glowing appearance. Josef Riedel played a major role in advancing this craft. He created special colors for the glass and named some of them after his wife, adding a personal touch to his work.
The production of uranium glass reached its height between the 1880s and the 1920s. Notable companies like James Powell’s Whitefriars Glass began marketing these striking pieces. The glass not only showcased human creativity but also demonstrated our ability to manipulate materials for aesthetic purposes.
Innovations in Uranium Glass Formulation
Uranium glass, known for its striking glow, has a fascinating history. In the early 1900s, makers discovered how to blend uranium dioxide into glass. This was a game-changer. They found that using about 2% uranium by weight brought out bright fluorescence and stable colors.
The methods of mixing ingredients improved over the years. Today, advanced machines ensure that uranium oxide is evenly distributed throughout the glass. This uniformity not only makes the glass look better, but it also reduces defects. Makers now often use depleted uranium in their formulas. This maintains the classic greenish-yellow glow while making the glass safer to handle.
Modern annealing techniques have also changed the game. These processes reduce thermal stress in the glass, making it stronger and less likely to crack.
Plus, artists and manufacturers have started to experiment with different colorants and additives. This exploration has led to new, vibrant shades like deep blues and soft pinks, which also glow beautifully under ultraviolet light.
Advanced Glassblowing Techniques for Uranium Glass
Uranium glass has a fascinating history that traces back to the early 19th century. This glass, known for its striking green and yellow hues, contains uranium oxide, which gives it its unique fluorescence. In the beginning, glassmakers experimented with uranium compounds as a way to enhance color and brightness in their creations.
Over time, the manufacturing techniques for uranium glass evolved. Early artisans relied heavily on traditional methods, where they heated silica and uranium oxide to high temperatures. They carefully controlled the heat, knowing that even slight variations could change the glass’s color. This precision was crucial for achieving the vibrant shades that collectors admire today.
As the glass industry progressed, innovative techniques emerged. Electric furnaces became popular, allowing for better temperature regulation and consistency. Glassmakers began to use complex molds and advanced blowing techniques. They layered colored glass over a uranium glass core, resulting in stunning visual effects. This combination of old and new methods helped artisans create pieces that captured attention and conveyed elegance.
Uranium glass saw a surge in popularity during the late 19th and early 20th centuries. It was often used in decorative items and tableware. People were drawn to its unique glow under ultraviolet light. However, concerns over uranium’s radioactivity emerged later, leading to a decline in its use.
Today, uranium glass is once again appreciated for its artistic value. Collectors and enthusiasts enjoy its historical significance and aesthetic appeal. Modern glass artists continue to explore this medium, combining techniques from the past with contemporary methods. The legacy of uranium glass lives on, showcasing the creativity and craftsmanship of glassmakers throughout history.
Molding and Casting Innovations in Uranium Glass Production
Uranium glass has a rich history that dates back to the early 19th century. Initially, glassmakers used uranium to give glass a vibrant green color and to create a unique glow under ultraviolet light.
Over time, the manufacturing techniques evolved significantly. Artisans began using precision molds to create more detailed shapes. This change allowed for the production of glass pieces that weren’t only beautiful but also consistent in quality.
The introduction of advanced casting methods like press molding and slip casting opened new doors for creativity. These techniques let manufacturers design both functional and decorative items with unique textures and finishes.
The impact of these developments has been profound. They’ve changed the way uranium glass is made, enhancing both its artistry and quality.
Today, collectors and enthusiasts appreciate the intricate designs and vibrant colors that modern techniques can achieve.
Precision Mold Techniques
Uranium glass has a long history, dating back to the 1830s in Europe. This unique glass material contains small amounts of uranium, which gives it a distinctive glow under ultraviolet light. Over the years, artisans have experimented with various techniques to create beautiful and functional pieces.
In recent times, innovations in manufacturing techniques have revolutionized the way uranium glass is produced. With the rise of computer-aided design, glassmakers can now craft intricate patterns and shapes. This technology allows for a level of detail that was previously unattainable.
The new precision molds not only enhance design complexity but also minimize waste. This shift in production methods increases efficiency and profitability. By carefully controlling the amount of uranium oxide in the glass, makers achieve vibrant colors and striking fluorescence.
Automated molding systems further contribute to this evolution. They streamline the production process and significantly boost output. Even with higher volumes, the quality of the glass remains exceptional. Durable materials like heat-resistant ceramics are used in molds, extending their lifespan and performance.
These advancements in manufacturing techniques have given artisans greater control over the glass-making process. As a result, uranium glass pieces today reflect a higher level of craftsmanship than ever before. The combination of history and modern technology continues to shape this fascinating art form.
Advanced Casting Methods
Uranium glass, also known as vaseline glass, has a fascinating history that intertwines with the evolution of manufacturing techniques. In the early days, craftsmen relied on simple molds and rudimentary methods. They created pieces by hand, which often resulted in unique shapes but inconsistent quality.
As time went on, advancements in technology began to change the game. The introduction of precision molds allowed for more intricate designs. This meant artisans could create beautiful patterns and details that captivated collectors. The use of temperature control in the melting process also played a crucial role. It ensured that the glass maintained its vibrant colors and glow, which are hallmarks of uranium glass.
In recent years, computer-aided design (CAD) has revolutionized how manufacturers approach production. This technology brings a new level of accuracy and consistency to the casting process. Mass production became feasible without compromising the artistry that collectors value.
New techniques, like pressure casting and slip casting, emerged. These methods enable the efficient creation of uranium glass items on a larger scale, all while upholding high standards of craftsmanship and safety.
Using depleted uranium in the glassmaking process has been a key factor in achieving that signature luminescent quality. Collectors appreciate the distinct glow and vibrant hues that come from this material.
At the same time, manufacturers prioritize safety, adhering to strict regulations concerning radiation. This balance between beauty and safety continues to drive the development of uranium glass, making it a cherished item among enthusiasts and collectors alike.
Technological Improvements in Glass Coloring Processes
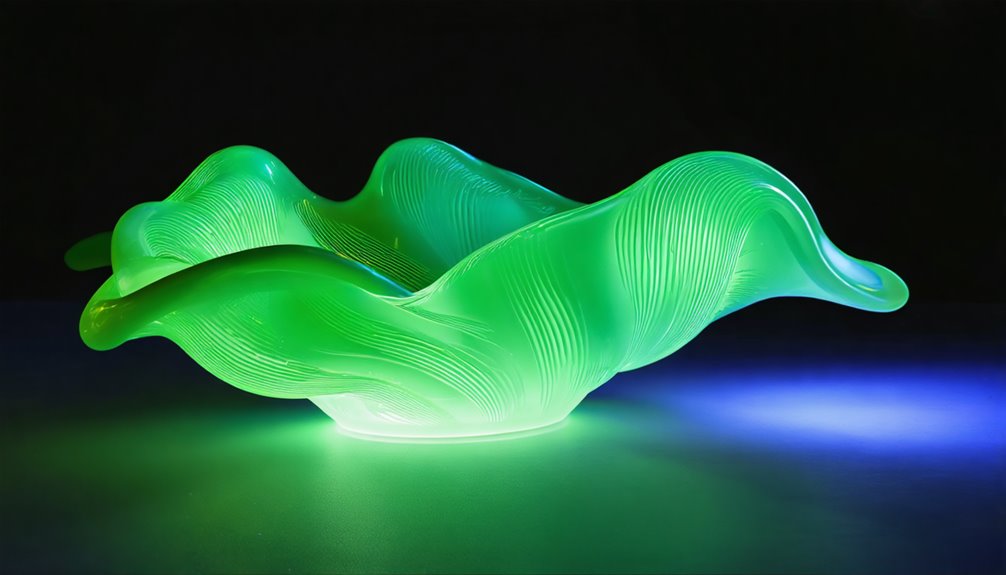
Since the early 19th century, glass coloring methods have changed a lot due to new technologies. One major change happened in the 1830s when uranium oxide was introduced as a coloring agent. This allowed glassmakers to create uranium glass, which has eye-catching yellow-green colors and interesting fluorescent properties. Collectors find these features very appealing.
The introduction of uranium oxide in the 1830s revolutionized glassmaking by creating vibrant, fluorescent uranium glass that continues to captivate collectors today.
Advancements in glass mixing and furnace design have increased production efficiency. Manufacturers can now produce uranium glass on a large scale while maintaining high quality and clarity. Following modern safety regulations, manufacturers can now use depleted uranium. This makes the production process safer while still retaining powerful coloring effects.
Several important developments have contributed to these improvements:
- Accurate blending of uranium oxide
- Enhanced glass clarity
- Managed oxidation states for better effects
- Improved temperature control in furnaces
- Use of depleted uranium to ensure safety
These advancements in manufacturing techniques have shaped the history of uranium glass and its production.
Achieving Precision in Uranium Glass Coloration
Uranium glass has a rich history that reflects advancements in glassmaking techniques. Early glassmakers experimented with uranium compounds to create vibrant colors. This experimentation laid the groundwork for modern practices in coloration.
In the late 19th century, the introduction of uranium oxide in glassmaking became popular. This innovation allowed artisans to produce striking green and yellow hues. The unique fluorescence of uranium glass captured the imagination of many collectors and enthusiasts.
As technology progressed, glassmakers learned to manipulate the oxidation states of uranium. This skill enabled them to achieve precise color effects. By adding specific metal ions, they could create a range of shades, from soft yellows to deep greens. Each color had its own fluorescence properties, adding to the allure of uranium glass.
Glass furnaces also evolved over time. Modern furnaces provide better control over melting temperatures and processes. This control ensures that each piece of glass is consistent in color and quality.
The combination of these advancements has led to a renaissance in uranium glass production. Today, the techniques used in uranium glass manufacturing highlight the importance of precision. The ability to measure uranium oxide accurately and manage oxidation processes has transformed the craft.
Now, glassmakers can achieve beautiful, uniform pieces that honor the rich history of this unique material.
Evolution of Safety Protocols in Uranium Glass Manufacturing
Uranium glass, known for its striking green hue and unique glow under ultraviolet light, has a long history intertwined with safety measures. The glass contains radioactive materials, which has prompted the evolution of safety protocols in its manufacturing. Over time, these protocols have become more rigorous to protect both workers and consumers.
Manufacturers now primarily use depleted uranium, which significantly lowers radiation exposure. This shift has made the production of uranium glass safer. The current standards limit the uranium content to about 1-2% by weight for decorative glass. This ensures that the glass remains visually appealing while minimizing health risks.
Worker safety is a top priority. Extensive training is provided to ensure that employees handle radioactive materials correctly. Regular inspections are conducted to verify that uranium doesn’t leach into food or liquids. Compliance with regulatory guidelines is mandatory, helping to maintain safety and legality in production.
Monitoring is continuous. Manufacturers regularly assess their processes and practices to uphold the highest safety standards. This commitment to safety reflects the industry’s response to past challenges and demonstrates a dedication to protecting everyone involved, from workers to consumers.
Radiation Monitoring Technologies for Uranium Glass
Uranium glass, often called Vaseline glass, has a rich history that dates back to the early 19th century. Its unique greenish-yellow hue comes from the addition of uranium oxide during manufacturing. This glass became popular in the Victorian era for both decorative and practical uses. People admired its striking appearance and its ability to fluoresce under ultraviolet light.
As manufacturing techniques evolved, artisans learned to create uranium glass with various designs and patterns. The glassblowing methods used in the 1800s allowed for intricate shapes. By the early 20th century, uranium glass was mass-produced, making it accessible to a broader audience. However, during World War II, the focus shifted, and the production of uranium glass decreased significantly.
Despite its decline, interest in uranium glass revived in the late 20th century, fueled by collectors and enthusiasts. They appreciate its historical context and the craftsmanship involved in its creation. It’s important to note that while uranium glass is generally safe, it does emit low levels of radiation. Therefore, monitoring radiation exposure is essential, particularly for those who handle it regularly.
Today, collectors and researchers use various tools to assess radiation levels in uranium glass. Devices like Geiger counters and scintillation detectors help ensure safety by measuring alpha, beta, and gamma radiation. These advancements in monitoring technology allow for real-time data collection, helping users manage any potential risks effectively.
Enhancing Glass Clarity and Quality Through Modern Techniques
Uranium glass, also known as Vaseline glass, has a fascinating history rooted in glassmaking techniques. Over the years, the process of creating this unique glass has evolved significantly. Early glassmakers used uranium to add a vibrant green or yellow hue to their products. This method not only enhanced the visual appeal but also increased the glass’s ability to fluoresce under ultraviolet light.
Modern advancements in manufacturing have taken uranium glass to another level. Today, glassmakers employ innovative techniques that focus on purity and consistency. By controlling temperature precisely, they can minimize impurities and defects. This results in clearer glass with a more uniform color.
The polishing and refining processes have also improved. With new machinery and methods, the surface of the glass becomes incredibly smooth. This not only enhances the aesthetic quality but also improves the glass’s durability.
As a result, contemporary uranium glass stands out for its clarity and resilience, showcasing the remarkable progress made in glassmaking technology.
Innovations in Glass Purity
Uranium glass has a rich history that traces back to the early 19th century. Manufacturers began experimenting with uranium as a coloring agent, leading to unique green and yellow hues. Over the years, techniques evolved, and the purity of glass became a significant focus.
In the quest for clarity, innovative purification methods emerged. These techniques allowed makers to refine the glass, removing unwanted elements that could mar its appearance. Advanced filtration systems played a vital role in this process, ensuring that bubbles and inclusions were minimized. The result was a smoother, more appealing surface.
Controlling the chemical composition of uranium glass became essential. By carefully selecting and mixing raw materials, producers achieved a consistent quality. This precision not only improved clarity but also enhanced the glass’s fluorescent properties, making it even more attractive to collectors and enthusiasts.
Temperature control during melting is another important factor. It ensures that all components blend uniformly, contributing to the stunning brilliance of the final product. Additionally, specialized additives and coatings were developed. These enhancements improved light transmission, allowing light to pass through with remarkable clarity.
The evolution of manufacturing techniques has transformed uranium glass into a sought-after item. Its beauty and uniqueness continue to captivate those who appreciate its history and craftsmanship.
Advanced Clarity Enhancement Methods
Uranium glass has a fascinating history that dates back to the 1830s. Initially, glassmakers created this unique glass by adding uranium salts to the glass mixture. This process gave the glass a distinctive green or yellow hue and made it glow under ultraviolet light.
Over the years, manufacturers have improved their techniques for creating uranium glass. They began using high-purity silica, which helps to minimize impurities. This change leads to clearer and more attractive glass. Special additives were also introduced, enhancing the optical properties and overall transparency of the final product.
Polishing methods evolved, too. Glassmakers started using advanced abrasives and automated machinery, which allowed them to achieve smoother and more polished finishes. This innovation not only improved the aesthetic appeal but also showcased the craftsmanship involved in making uranium glass.
Another significant development is the use of ion-exchange strengthening. This technique helps to reinforce the glass, making it more durable while keeping it clear. Vacuum melting also became a standard practice, effectively removing air bubbles that could mar the glass’s beauty.
With modern technology, manufacturers can control the melting and forming processes with high precision. This ensures consistent thickness and temperature, which is vital for quality.
Lastly, new coating technologies have brought even more advantages. Anti-reflective and hydrophobic coatings protect the glass and enhance its visual appeal. These advancements make uranium glass not just beautiful but also practical for everyday use.
Automation in Modern Uranium Glass Production
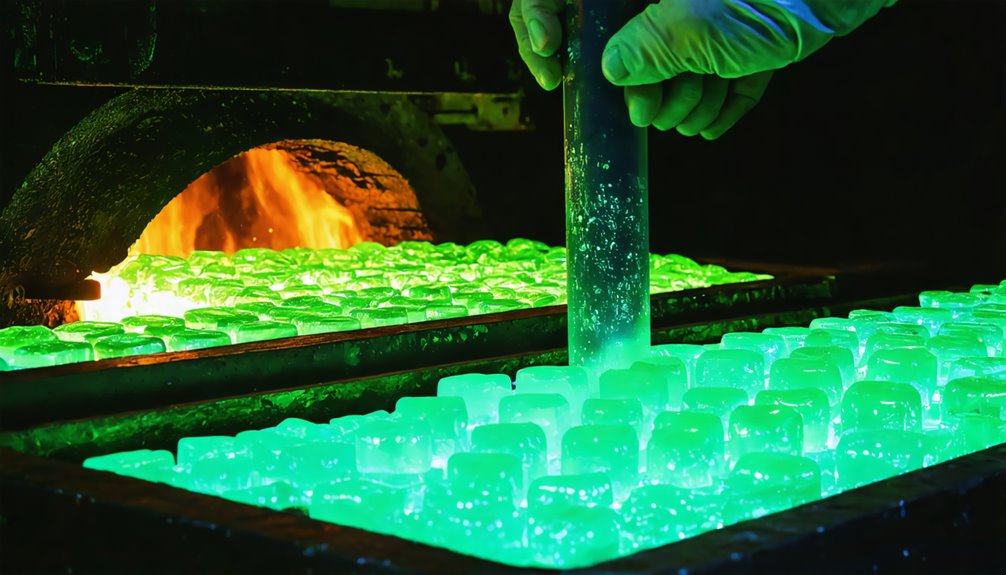
Uranium glass has a fascinating history that reveals how manufacturing techniques have evolved over time. Initially, skilled artisans created this unique glass using traditional methods. They relied on their expertise to mix raw materials and shape the glass by hand. This craftsmanship resulted in beautiful pieces, but production was slow and inconsistent.
As technology progressed, manufacturers started to adopt new techniques. Automation began to play a crucial role in uranium glass production. It brought about notable changes that improved efficiency and quality. For example, robotic arms now handle the mixing of raw materials with precision. This ensures that the vibrant colors and quality of the glass are uniform across the board.
Moreover, advanced machinery helps in the melting and shaping processes. This automation speeds up production while maintaining the essence of traditional craftsmanship. Manufacturers can now create intricate designs at a larger scale without compromising quality.
Automation also enhances quality control. Sensors monitor the production process, allowing for rigorous checks that weren’t possible in earlier methods. This ensures that every piece of uranium glass meets high standards.
The Role of Uranium Glass in Contemporary Art and Design
Uranium glass has a rich history that dates back to the early 19th century. It first appeared in Europe, where glassmakers began to experiment with adding uranium compounds to glass mixtures. This practice aimed to create a vibrant green or yellow color. The unique properties of uranium glass became popular, especially during the Victorian era.
Emerging in 19th-century Europe, uranium glass captivated Victorian audiences with its distinctive, vibrant green and yellow hues.
Manufacturing techniques evolved over time. Early methods relied on simple mixing, but as technology advanced, glassmakers developed more sophisticated processes. They learned to control the uranium content, ensuring safety standards were met. Companies like Fenton and Mosser became well-known for their skillful production of uranium glass. They combined traditional craftsmanship with modern safety regulations, resulting in beautiful pieces that collectors cherish.
Uranium glass isn’t just a collectible. It has also found a place in contemporary art and design. Artists appreciate its glowing fluorescence under ultraviolet light. This striking feature adds an engaging element to their work, creating installations that captivate viewers. The interplay of light and color in uranium glass pieces evokes feelings of nostalgia and curiosity about industrial history.
Exhibitions featuring uranium glass highlight its dual role. They showcase the glass as both a collectible and an artistic medium. This blend of art and science fosters new collaborations, pushing the boundaries of creativity. The future of uranium glass looks promising, as artists continue to explore its potential.
Revival of Uranium Glass Popularity in the Modern Era
In the 1990s, the end of Cold War restrictions led to a revival of interest in uranium glass. Artists, glassmakers, and collectors began to appreciate its unique qualities. I’ve seen this trend grow as people are drawn to the charm of these glowing pieces. The revival is fueled by a mix of nostalgia and the desire for striking decorative items.
Manufacturers like Fenton and Mosser have improved glassmaking techniques. They create detailed designs and vibrant colors while meeting modern safety standards. This commitment to quality excites collectors.
Several factors contribute to the ongoing fascination with uranium glass. Online marketplaces make it easier to find rare items. Active groups, such as Vaseline Glass Collectors, Inc., provide valuable information and support for enthusiasts. Events like antique shows highlight unique pieces that collectors seek.
Prices for uranium glass vary widely, depending on how rare the items are. Collectors value the distinctive look and historical background of uranium glass. Its story adds depth to its appeal, making it a cherished collectible in today’s market.
Environmental Impact and Sustainability in Uranium Glassmaking
Uranium glass has a rich history that dates back to the 1830s. It was first created by glassmakers in Europe who discovered that adding uranium oxide to glass produced a unique, vibrant green or yellow color. This glass became popular for decorative items and tableware.
Over the years, the techniques for making uranium glass evolved. Early glassmakers relied on simple methods, but as the demand grew, they developed more advanced techniques. The introduction of electric furnaces in the late 19th century allowed for better temperature control. This improvement led to more consistent quality in the glass produced.
In the 20th century, uranium glass saw a surge in popularity, especially during the 1930s to the 1950s. During this time, manufacturers began using uranium in their glass to enhance its glow under ultraviolet light. This glowing effect made uranium glass particularly appealing to collectors and the general public.
However, as awareness of nuclear materials’ potential risks grew, so did concerns about uranium glass’s safety. Manufacturers adapted by implementing stricter safety measures. They focused on reducing uranium content and ensuring proper handling during production.
Today, the legacy of uranium glass continues. Modern manufacturers are more mindful of the environmental impact of their production processes. Many use recycled uranium glass to lessen waste and energy use.
Advances in recycling technology also contribute to this shift, allowing for effective repurposing of uranium glass. This focus on sustainability helps create a safer industry while preserving the unique history of uranium glass.
Uranium Waste Management
Uranium glass, also known as Vaseline glass, has a unique history that dates back to the 1830s. Early glassmakers discovered that adding uranium oxide to glass created a striking green or yellow hue. This innovation quickly gained popularity, especially in the late 19th and early 20th centuries. The glass shimmered under UV light, drawing attention from collectors and everyday users alike.
Manufacturing techniques evolved over time. Initially, artisans crafted uranium glass by hand, but as demand grew, factories adopted industrial methods. These advancements allowed for mass production, making uranium glass accessible to a broader audience. The use of uranium also contributed to the glass’s distinctive glow, which became a novelty in households and cafes.
Despite its appeal, the radioactive nature of uranium raised concerns. As awareness of radiation risks increased, glassmakers faced pressure to modify their methods. Some shifted to using depleted uranium, which has lower radioactivity. This change aimed to reduce health risks while maintaining the glass’s unique properties.
Today, the legacy of uranium glass continues. Collectors value it for its historical significance and aesthetic qualities. The development of manufacturing techniques reflects a blend of artistry and science, showcasing how innovation can shape a product’s journey.
Understanding this history emphasizes the importance of responsible practices in glassmaking.
Sustainable Glass Production
Uranium glass has a rich history, fascinating many collectors due to its unique glow and vintage appeal. This type of glass, often called “Vaseline glass,” was popular in the 19th and early 20th centuries. It contains small amounts of uranium, which gives it a distinct greenish hue and allows it to fluoresce under ultraviolet light.
Over the years, glassmakers have improved their techniques. Today, there’s a growing focus on sustainable practices. Modern manufacturers incorporate recycled materials and enhance energy efficiency. They aim to lessen the environmental footprint of glass production. Using depleted uranium, they can also help manage low-level radioactive waste. This approach supports the circular economy, where waste is reused in new products.
Recent advancements in glassmaking allow for a lower uranium content, typically around 2%. This change reduces the potential health risks associated with higher levels of radioactivity.
Furthermore, cleaner production methods have emerged. These include using renewable energy sources and minimizing water consumption. Such practices improve sustainability without sacrificing the quality of the glass.
Regulatory frameworks now play a crucial role in this industry. They set clear limits on uranium content. These rules promote the use of safe and sustainable materials in decorative glassware.
Recycling Uranium Glass
Uranium glass, also known as Vaseline glass, has an intriguing history. It began in the early 19th century when glassmakers experimented with different materials to create unique effects. The use of uranium oxide in glass introduced a vibrant green or yellow color and made the glass glow under ultraviolet light.
Manufacturing techniques for uranium glass evolved over the years. In the late 1800s, companies like Fenton and McKee started producing decorative items using this special glass. They utilized uranium to enhance the visual appeal of their products. This innovation captured the attention of collectors and everyday consumers alike.
The challenges of recycling uranium glass are notable. Its radioactive properties require careful handling to avoid health risks. Separating uranium glass from regular glass is essential to prevent contamination. Moreover, only a few facilities can process these materials safely.
There is also limited demand for recycled uranium glass products. Many people are unaware of the glass’s historic significance or its potential for decorative use. Some manufacturers are working hard to create attractive items from recycled uranium glass, combining the charm of vintage pieces with modern environmental efforts.
Despite the obstacles, the innovative spirit of some artisans shines through. They’re developing unique decorative items that honor the past while promoting sustainability. This balance of history and environmental responsibility is crucial for the future of uranium glass.
Collecting Uranium Glass: Technological Effects on Market Trends
Uranium glass has a fascinating history that dates back to the 1830s. Initially, it was used for its unique green color and fluorescence. Manufacturers like Fenton and Mosser began incorporating uranium into their glass mixes, which gave the glass a captivating glow under ultraviolet light. This innovation changed the way collectors viewed and valued these pieces.
Since the 1830s, uranium glass captivated collectors with its distinctive green hue and mesmerizing glow under ultraviolet light, transforming glassmaking forever.
After the Cold War, production of uranium glass saw a revival. This renewed interest led to a surge in creativity among glassmakers. They began crafting intricate designs that appealed to both new collectors and seasoned enthusiasts. The bright, luminescent qualities of uranium glass made it stand out in the market.
The rise of retro collectibles also played a role in boosting demand for uranium glass. Items from the late 19th and early 20th centuries, considered rare, became highly sought after. Collectors sought these unique pieces, driving prices higher.
With the internet, collectors now have access to vast resources. Online communities help determine authenticity and value. This support has transformed collecting uranium glass into a rewarding hobby. Collectors can build impressive collections that reflect their passion while influencing market trends.
Future Trends and Innovations in Uranium Glass Technology
Uranium glass has a fascinating history that dates back to the early 19th century. Originally, glassmakers used uranium oxide to create colorful glassware. This glass, known for its vibrant green and yellow hues, became popular in the Victorian era. It wasn’t just beautiful; it also glowed under ultraviolet light due to the uranium content.
Over the years, manufacturing techniques evolved. Early glassmakers relied on traditional methods, but as technology advanced, so did the processes. The introduction of better mixing techniques and the use of additives allowed for the creation of stronger and more vivid glass. This meant that artists could experiment with more complex designs and colors.
In recent times, there’s been a shift towards sustainability in uranium glass production. Manufacturers are now looking for safe ways to use depleted uranium, reducing the environmental impact. This change reflects a growing awareness of the need for responsible practices in all industries, including glassmaking.
The collaboration between artists and glassmakers has also played a crucial role in the development of uranium glass. By combining traditional skills with modern techniques, they create unique pieces that are both artistic and functional. These partnerships help push the boundaries of what uranium glass can be.
As we move forward, the focus on durable and visually striking designs will likely continue. Innovations in the field promise to enhance the fluorescent properties of uranium glass even further. This ongoing development ensures that uranium glass remains an exciting area of exploration for both creators and collectors.
Sustainable Uranium Glass Production
Uranium glass has a rich history that captivates many collectors. This glass, which glows under ultraviolet light, first gained popularity in the late 19th century. The use of uranium in glassmaking was a creative way to produce vibrant colors and unique effects. However, as time went on, concerns about safety and environmental impact grew.
The manufacturing techniques for uranium glass have evolved over the years. Early glassmakers relied on natural uranium, which posed health risks. Today, the industry has shifted towards using depleted uranium. This change helps reduce potential hazards while still allowing for the beautiful characteristics that collectors love.
Recycled glass has also become an important part of the production process. By incorporating recycled materials, manufacturers cut down on waste and lessen their ecological footprint. This method isn’t only eco-friendly but also supports a circular economy.
Safety remains a top priority in uranium glass production. Glassmakers have adopted precise measurement techniques to ensure compliance with safety regulations. This attention to detail helps protect both workers and consumers.
Innovations in coloring techniques have emerged as well. Researchers are looking for alternative colorants that mimic the distinctive fluorescent properties of uranium without using the element itself. This approach could further enhance the safety of the glass while maintaining its aesthetic appeal.
Collaboration with environmental organizations is crucial. These partnerships help establish responsible sourcing guidelines that promote sustainable practices in the industry. By working together, glassmakers can create a future that honors both tradition and environmental stewardship.
Uranium glass continues to evolve, blending history with modern manufacturing techniques. Its journey reflects a commitment to safety, sustainability, and beauty.
Enhanced Fluorescent Properties
Uranium glass has a rich history that reflects the evolution of manufacturing techniques over the years. Initially, glassmakers used basic methods to create this unique material. They added uranium oxide to glass mixtures, which gave it a distinct greenish hue and a faint glow under UV light.
As demand grew, artisans began experimenting with different methods. They found that precise mixing of uranium oxide led to uniform distribution throughout the glass. This resulted in a more consistent and striking fluorescent glow when exposed to UV light.
In the 20th century, the introduction of controlled cooling processes allowed for greater stability in the glass. This not only maintained the vibrant glow but also reduced defects. Manufacturers began to blend uranium with rare earth elements, creating unique color variations that appealed to collectors.
In recent years, advanced UV detection technology has played a crucial role in ensuring safety standards. This technology helps identify the levels of radioactivity in uranium glass, making it safer for consumers. Additionally, many manufacturers have adopted eco-friendly practices, creating sustainable products that still possess the powerful visual impact that uranium glass is known for.
The journey of uranium glass showcases the blend of art and science. Each advancement in manufacturing techniques has contributed to its allure, making it a fascinating topic for both collectors and historians.
Frequently Asked Questions
Why Is Uranium Glass Not Used Anymore?
Uranium glass, also known as Vaseline glass, was once popular for its unique greenish hue and its ability to fluoresce under ultraviolet light. It gained fame in the late 19th and early 20th centuries as manufacturers experimented with adding uranium to glass to enhance its color and appeal. However, over time, various factors led to a decline in its production.
Health concerns became a significant reason for its decreased use. Uranium is a radioactive element, and prolonged exposure can pose health risks. As awareness of radiation and its effects grew, the public began to worry about the safety of uranium glass items. This fear was amplified by strict safety regulations that emerged in the mid-20th century, making it difficult for manufacturers to continue producing uranium glass without facing legal challenges.
Negative public perception played a role too. Many people viewed uranium glass as potentially dangerous, associating it with radiation hazards. This fear overshadowed its artistic value, causing a shift in how collectors and enthusiasts regarded it. Instead of being seen as a novel and desirable material, uranium glass became somewhat stigmatized.
As a result, the focus shifted to the artistic value of uranium glass. Collectors began to appreciate its historical significance and unique craftsmanship rather than its utility. Today, uranium glass is mainly sought after by collectors who admire its beauty and rarity.
Is New Uranium Glass Being Made?
Uranium glass, also known as Vaseline glass, has a fascinating history. It originated in the 1830s when glassmakers began adding uranium oxide to their glass mixtures. This addition created a vibrant yellow-green color and made the glass fluoresce under ultraviolet light.
Over the years, the manufacturing techniques for uranium glass have evolved. Early methods were simple and relied on traditional glass-blowing practices. As technology advanced, manufacturers adopted new techniques that allowed for more intricate designs and shapes. This innovation led to the production of unique pieces that appealed to collectors and enthusiasts.
Today, there is a renewed interest in uranium glass. Artisans are experimenting with modern techniques while respecting the historical significance of this material. Safety measures are carefully observed during the production process to ensure that the glass is safe for use. The demand for uranium glass has risen, driven by collectors seeking distinctive items for their displays.
The environmental impact of producing uranium glass is minimal compared to other materials. The process mainly involves recycling existing glass and using small amounts of uranium, which is carefully controlled. As a result, new uranium glass is being made, combining artistic flair with a rich historical background.
Why Is Uranium Glass Illegal?
Uranium glass, often called Vaseline glass, has a rich history that dates back to the early 19th century. It gained popularity due to its striking green hue and ability to glow under ultraviolet light. Manufacturers used uranium oxide as a colorant, which gave the glass its unique appearance.
Over time, advancements in manufacturing techniques allowed artisans to create intricate designs and shapes. The glass became a favorite among collectors. However, the use of uranium in glass-making raised concerns.
Radiation levels in uranium glass are low, but they can still pose risks. Because of this, safety regulations emerged. These laws limit the production and sale of uranium glass. Today, it is mostly of interest to collectors, rather than something people use in their daily lives.
Environmental concerns also play a role in its restricted use. The mining and processing of uranium can have harmful effects. As a result, responsible practices in glass production and waste management became crucial.
Why Was Uranium Used in Glass Making?
Uranium was used in glass making due to its unique properties that created striking colors. This type of glass, often called uranium glass or Vaseline glass, became popular in the 19th and early 20th centuries. Manufacturers discovered that adding small amounts of uranium oxide to glass melted at high temperatures resulted in vibrant greens and yellows.
The development of this technique coincided with advancements in glass manufacturing. Factories utilized uranium to enhance the aesthetic appeal of their products. This glass was not only beautiful but also glowed under ultraviolet light, making it a collector’s item.
However, the health risks associated with uranium’s radioactivity prompted concerns. By the mid-20th century, many glassmakers began to phase out uranium in their products. Despite this, uranium glass remains a fascinating part of history. Today, collectors appreciate its unique characteristics and historical significance.
Conclusion
Uranium glass has a fascinating history, marked by both creativity and science. This unique type of glass, which glows under ultraviolet light, was first made in the early 19th century. Craftsmen used uranium to give the glass a striking green or yellow hue. Over the years, glassmakers experimented with different techniques to enhance the clarity and color of uranium glass.
Manufacturing techniques have greatly evolved since those early days. Today, advanced technology allows for more precise glass formulation and coloring methods. This modern approach not only improves the quality of uranium glass but also expands its design possibilities. As a result, it has found a renewed place in the market, appealing to both collectors and new enthusiasts.
Sustainability plays a significant role in today’s production practices. As we embrace innovation, it’s crucial to remember the heritage of uranium glass. Responsible methods ensure that this art form can thrive for generations to come. By blending traditional craftsmanship with contemporary techniques, we can keep the charm of uranium glass alive while being mindful of our planet.