The Evolution of Uranium Glass Production Methods
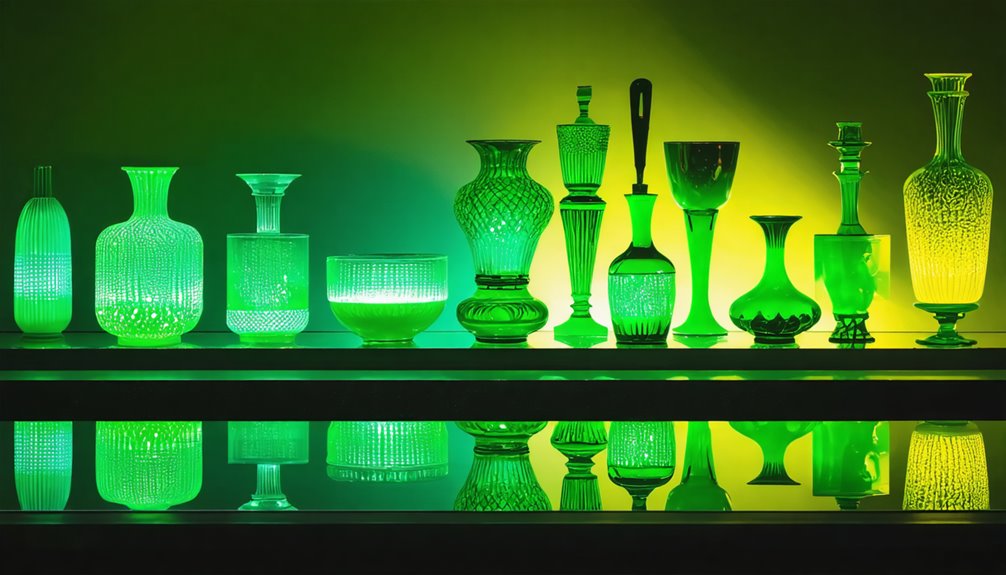
The history of uranium glass is fascinating and shows how manufacturing techniques have changed. It all started in the 19th century when skilled artisans began to experiment with uranium oxide. They wanted to create glass with unique and vibrant colors.
With the rise of industrialization in the 1830s, production methods changed. Factories began using molds and machines. This shift allowed them to produce more glass than ever before. The Victorian era brought in intricate designs and bright colors, making uranium glass even more popular.
However, global events like World War II and the Cold War affected uranium availability. These restrictions pushed manufacturers to innovate and find new ways to work with uranium.
Today, the methods for producing uranium glass are much safer. Manufacturers now use depleted uranium, which is less hazardous. Strict safety regulations are in place to protect workers and consumers. Additionally, there is a focus on sustainability in the production process. Artists are also exploring new techniques, keeping this unique craft alive and evolving.
Key Takeaways
Uranium glass production started in the early 1800s. At that time, makers used manual blending techniques. By the 1830s, they began to adopt industrial mold methods. This shift allowed for more consistent shapes and designs.
During the Victorian era, the craft of uranium glass really took off. Artisans developed intricate designs. They used refined molding, etching, and shaping processes to create stunning pieces. This period marked a high point in creativity and detail.
However, the Great Depression brought challenges. Economic pressures led to a need for simpler designs. Manufacturers focused on making affordable, mass-produced uranium glass items. Practicality became key during this tough time.
The events of World War II and the Cold War changed everything again. Scarcity of uranium meant that glass production dropped significantly. Manufacturers had to find new materials and techniques to keep their businesses alive. Innovation became crucial.
Today, uranium glassmaking has transformed once more. Modern techniques use depleted uranium, which is safer. Advanced safety protocols are now standard in production. Sustainability is also a focus, with many makers aiming for both art and function in their creations.
Early Techniques in Uranium Glass Creation
Uranium glass is a captivating material known for its vibrant yellow-green glow. It first appeared in the early 19th century when glassmakers started to experiment with uranium oxide. They blended uranium with sand and soda, creating beautiful visual effects.
The commercial production of uranium glass took off in Bohemia during the 1830s. This development followed Klaproth’s discovery of uranium compounds.
By the mid-1800s, craftsmen in Victorian England enhanced these techniques. They created intricate decorative pieces that glowed brilliantly under ultraviolet light.
Artisans also played with different metal oxides along with uranium. This experimentation led to various styles of uranium glass, including the popular Vaseline and custard glass.
The creativity and skill of these early glassmakers laid the foundation for the unique aesthetic of uranium glass.
Transition From Artisanal to Industrial Production
In the 1830s, glassmaking underwent a significant transformation. Victorian artisans, known for their detailed and handcrafted methods, faced a new era of industrialization. This shift began prominently in Bohemia. Glassmakers, eager for advancement, adopted industrial techniques. They started using uranium oxide, which produced a striking yellow-green glass known as uranium glass.
With the introduction of industrial molds and specialized machinery, glassmakers could produce items more quickly than ever before. This meant that decorative tableware and scientific instruments could be made in large quantities without sacrificing quality. Notable companies, such as Whitefriars Glass in the UK and Fenton Glass in the US, were quick to embrace these innovative methods. As a result, production volumes increased dramatically.
Production Method | Benefits Gained |
---|---|
Artisanal | Unique Pieces, Limited Quantity |
Industrial | Consistent Quality, Mass Production |
Result | Greater Market Power, Expanded Influence |
This evolution in manufacturing allowed companies to meet consumer demand efficiently. The industrial approach led to reliable products that could be produced on a large scale, reshaping the glassmaking industry and its market dynamics.
Influence of the Victorian Era on Manufacturing Methods
The Victorian Era had a significant effect on the production of uranium glass. During this time, manufacturers like Whitefriars Glass and Fenton Glass became captivated by intricate designs. They improved their molding techniques, which allowed them to create beautiful, detailed glass pieces on a larger scale. This was a big change in how glass was made.
Uranium oxide was a popular choice for glassmakers because it created vibrant yellow and green colors. These colors had a special quality; they glowed under ultraviolet light. This unique feature caught the attention of many buyers. The excitement around these glowing colors led to a surge in demand for uranium glass.
This growing interest transformed the glass industry. New glasshouses began to focus specifically on creating these bright and attractive items. As a result, the manufacturing methods evolved, leading to more innovative and stylish glass products.
The Victorian Era not only influenced consumer tastes but also played a crucial role in shaping the future of glassmaking.
Ornate Victorian Designs
During the Victorian era, glassmakers created stunning works of art using uranium. Companies like Whitefriars Glass and Fenton Glass stood out for their intricate designs and craftsmanship.
Victorian consumers loved unique and bold aesthetics. To meet this demand, manufacturers added uranium to their glassware. This gave the glass vibrant yellow and green colors. These hues became popular in items like vases, chandeliers, and other decorative pieces.
The designs were ornate. Glassmakers meticulously etched patterns and shaped the glass with care. Under ultraviolet light, uranium glass displayed eye-catching fluorescent qualities.
The advanced techniques of pressing and glassblowing were key to this art form. Victorian glassmakers set a high standard for creativity and innovation. Their work inspired future artisans and collectors, leaving a lasting legacy in the world of glass manufacturing.
Mass Production Techniques
Victorian artisans were known for their exceptional craftsmanship. However, their influence extended beyond just beautiful designs. In the Victorian Era, new mass production methods changed uranium glass items from rare treasures to common symbols of elegance and power. Factories like Whitefriars Glass and Fenton Glass took advantage of new techniques in mold-making and glass blowing. They also used machines that automated processes, which sped up production and lowered costs.
This shift to industrial methods meant that beautiful tableware and decorative items became widely available. People craved opulence and prestige, and these products filled that need.
Here’s how production changed during this time:
Production Aspect | Victorian Change |
---|---|
Mold-Making | Complex patterns, quick duplication |
Glass Blowing | Greater accuracy, intricate designs |
Automated Machinery | Lower expenses, improved productivity |
Production Volume | Greater supply, widespread appeal |
Consumer Accessibility | Affordable elegance, common use |
The advances in manufacturing made uranium glass accessible to more people. It shifted from being a luxury to an everyday item, enriching homes with its charm.
Coloration and Fluorescence
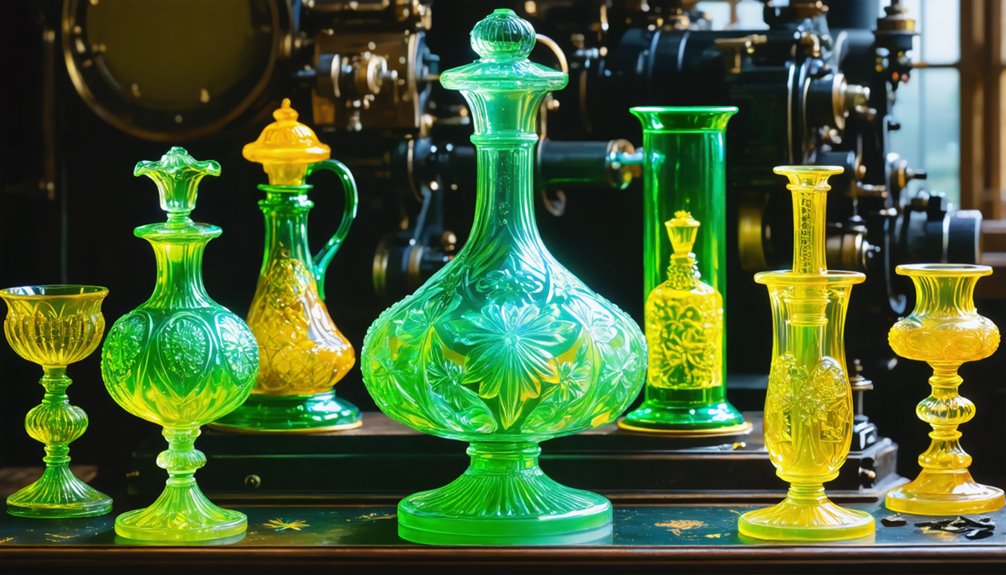
Uranium oxide was known as a glass colorant for some time. But it was during the Victorian era that glassmakers truly explored its potential. They learned how to add uranium oxide in precise amounts. This created bright yellow-green colors that captured the spirit of the time. The craftsmanship was ornate and detailed.
A fascinating discovery came in the mid-19th century. Uranium glass glowed brilliantly under ultraviolet light. This wasn’t just a scientific curiosity; it became a trend. People were drawn to the unique glow, making uranium glassware highly sought after. It shifted from being a novelty to a symbol of status.
Glassmakers like Whitefriars and Fenton embraced these techniques. They produced beautiful dinnerware and decorative pieces. The combination of vivid colors and striking fluorescence showcased their skill.
This innovation added to the reputation of Victorian glass artistry. It marked a significant development in manufacturing techniques, blending science with creativity.
Innovations in Glassmaking Technology
In the 19th century, glassmakers started adding uranium oxide to their glass mixtures. This change brought about bright yellow and green colors never seen before.
These innovations in glassmaking changed the craft significantly. Artisans created stunning pieces that stood out, becoming symbols of wealth and luxury.
With better furnaces and melting methods, glassmakers could mix uranium evenly in their glass. This control led to consistent quality and dazzling brightness in uranium glass.
The intricate designs of the Victorian era flourished, adding to the beauty and glow under ultraviolet light. As a result, uranium glass became a favorite among the wealthy, representing status and influence.
For anyone interested in this unique art, knowing about these manufacturing advances highlights the special charm of uranium glass.
Understanding its history enriches our appreciation for its beauty and the skill involved in its creation.
Uranium Glass Production During the Roaring Twenties
Uranium glass had a remarkable rise during the Roaring Twenties. This unique material, known for its striking glow under ultraviolet light, captivated many. It became a representation of luxury and style, showcasing the energy and innovation of the era.
Famous glassmakers like Fenton Glass in the United States and Whitefriars Glass in the United Kingdom developed advanced methods to produce this glass. They crafted beautiful items, such as intricate lampshades and elegant dinnerware, in vibrant yellow and green hues.
Initially, uranium glass was a luxury, enjoyed only by the wealthy. However, over time, it transitioned into more common glassware, making it accessible to a broader audience.
People began to appreciate the versatility of uranium glass. It allowed them to display their sophistication and taste in their everyday lives. The production techniques of the time helped meet this growing demand.
As a result, uranium glass became a bold symbol of status and prosperity during the Roaring Twenties. This period truly marked a significant development in the history of uranium glass manufacturing.
Adaptations in Manufacturing During the Great Depression
During the Great Depression, uranium glass manufacturers faced economic struggles. They decided to change their production methods. Instead of making fancy decorative items, they began creating simple, affordable household items like plates and bowls. This shift was necessary to meet the needs of consumers looking for budget-friendly options.
To keep costs down, glassmakers had to get creative. They changed the materials they used and simplified their designs. Despite these changes, they ensured that the glassware retained its unique fluorescent glow. This was important because it kept uranium glass appealing to buyers even in challenging times.
The adaptation of manufacturing techniques during this period helped uranium glass remain a popular choice. It transformed from a luxury item into an everyday necessity. Consumers appreciated the practicality and affordability, making uranium glass a staple in many homes.
This shift in focus not only supported manufacturers but also provided families with functional and attractive products during a difficult era.
Shift to Everyday Items
Uranium glass became popular for its beautiful decorative pieces. However, the Great Depression changed what people wanted. Families needed affordable and practical items. Manufacturers quickly adjusted their production. Instead of fancy vases and elaborate sculptures, they focused on everyday items like plates, bowls, and simple drinkware.
This change didn’t take away from uranium glass‘s charm. It made the glass more accessible for regular families. With its unique glow, it brightened homes during tough times. The new designs were simple and easy to make, which helped keep costs down. Manufacturers found a way to produce uranium glass efficiently while maintaining its special fluorescence.
Cost-saving Material Choices
During the Great Depression, uranium glass manufacturers had to change their approach due to economic challenges. They looked closely at their materials and production methods. Uranium was cheap and readily available. This made it a smart choice for glassmakers who wanted to keep producing affordable glass items during tough times.
Manufacturers took several steps to adapt:
- They reduced the use of costly raw materials and relied more on uranium.
- They simplified designs, cutting back on intricate details. This saved time and money.
- They used existing glassmaking techniques that were more efficient and cost-effective.
- They focused on practical shapes and styles. This appealed to consumers who were trying to save money.
These changes helped producers stay competitive in a difficult market. By using uranium and simplifying their processes, they continued to offer products that people wanted, even when times were hard.
Functional Design Trends
During the Great Depression, manufacturers faced tough times. They didn’t just change the materials they used; they also changed the designs of uranium glassware. Economic struggles pushed companies to move away from producing fancy, ornate items. Instead, they focused on creating practical and affordable pieces for everyday households.
Factories began crafting simple bowls, plates, and glassware. They used basic shapes and mass-production methods to keep costs down. This shift made uranium glass accessible to more people. It turned from a luxury item into something that families could use every day.
Despite the simpler designs, the unique fluorescence of the glass remained. This kept consumers interested and engaged. By prioritizing practicality and affordability, manufacturers ensured that uranium glassware continued to be produced.
It became a symbol of resilience during tough financial times. This focus on functionality over extravagance marked a significant change in manufacturing techniques, reflecting the needs of consumers in a challenging economy.
The Impact of World War II on Uranium Glassmaking
During World War II, uranium became a crucial resource. The U.S. government took control of uranium supplies. They directed these supplies exclusively toward the Manhattan Project, which aimed to develop atomic weapons. This action had immediate consequences for uranium glass production. Manufacturers found themselves without the necessary materials. As a result, the vibrant appeal of uranium glass faded. The focus shifted from decorative uses to military needs.
This shift impacted uranium glassmaking in four significant ways:
- Uranium glass manufacturing stopped completely.
- The government imposed strict control over uranium supply chains.
- Uranium’s role changed from decorative to military applications.
- There was a long-term scarcity of quality uranium, limiting access for the industry after the 1940s.
The development of manufacturing techniques for uranium glass had to adapt to these changes. Before the war, glassmakers experimented with different compositions. They found ways to create radiant colors and unique designs.
But as resources became limited, innovation slowed.
In the post-war period, the industry struggled to regain its footing. The focus on military applications left little room for creative glassmaking. Manufacturers had to find alternative materials and techniques. Some tried to replicate the look of uranium glass without using actual uranium. This challenge led to new developments in glassmaking.
Ultimately, the war reshaped the landscape of uranium glass. What was once a popular collectible became a relic of a different time. The vibrant colors and glowing effects were overshadowed by the pressing demands of wartime.
As the years passed, the allure of uranium glass remained, but its production faced significant hurdles.
Post-War Revival and Technological Advancements
After World War II, restrictions on uranium glass production eased. The Cold War brought a new set of regulations. Manufacturers had to be cautious about sourcing uranium.
At the same time, innovative glassmaking techniques emerged. Artisans created more detailed and colorful designs than ever before.
New safety measures also played a role. Incorporating depleted uranium helped lower radioactivity concerns. This made uranium glass safer for both collectors and craftspeople.
As a result, interest in uranium glass grew once again. Many people appreciated its unique glow and aesthetic appeal.
Overall, the post-war period marked a significant turning point in the history of uranium glass. Advances in manufacturing techniques and safety made a comeback possible.
Collectors began to seek out these vibrant pieces, leading to a revival of interest in this fascinating material.
Cold War Production Impact
Uranium glass experienced a notable comeback after the Cold War ended. This revival happened because government restrictions on uranium use became less strict. Before that, making uranium glass was tough. Strict rules were in place, making it hard for companies to work with uranium. Once those rules relaxed, manufacturers like Fenton and Mosser saw a chance to bring this unique glass back to life.
Several key reasons fueled this resurgence. First, new technologies improved the glass’s clarity and bright glow. Second, the uranium content decreased significantly. In the past, it was as high as 25%, but now it often sits safely between 0.1% and 2%. Third, regulatory bodies stepped in to ensure safety, which helped build trust among consumers. Lastly, many collectors sought out these colorful pieces. This demand encouraged manufacturers to create new styles that blended classic designs with modern flair.
The history of uranium glass reflects changing manufacturing techniques over time. As the market shifted, so did the ways glassmakers approached their craft. They combined innovation with tradition, leading to fresh designs that appeal to both collectors and casual buyers.
This evolution showcases how the glass industry adapts to new circumstances while honoring its rich past.
Modern Glassmaking Techniques
Uranium glass has a fascinating history. Its production saw a revival in the late 20th century. Since then, several key advancements have improved its manufacturing process. Companies like Fenton and Mosser have adopted modern glassmaking techniques that enhance both safety and design.
One major change is the use of depleted uranium. This approach reduces the glass’s radioactivity while still maintaining its captivating glow. By employing advanced melting and molding processes, artisans can now create intricate patterns and vibrant colors. This has made uranium glass even more desirable for collectors.
Controlled environments during production ensure that the glass is uniform. This eliminates many inconsistencies that plagued earlier methods. Additionally, the integration of UV monitoring technology allows manufacturers to adjust the uranium content in real-time. This ensures compliance with safety regulations without compromising the aesthetic qualities of the glass.
Advancements in Safety Measures
Uranium glass, also known as Vaseline glass, saw a resurgence in interest after World War II. The introduction of depleted uranium played a significant role in improving safety measures in its production. This shift was vital for collectors and manufacturers, allowing them to enjoy the unique qualities of these glass pieces without excessive concern.
Manufacturers began using advanced techniques to enhance safety. The integration of depleted uranium notably decreased radioactivity levels. This made the glass safer to handle. Rigorous safety protocols were established during production to ensure that workers and consumers were protected.
Geiger counters became essential tools in the manufacturing process. These devices measure radiation accurately, allowing glassmakers to monitor levels consistently. This attention to detail ensured compliance with strict regulatory standards.
Additionally, resources became available to educate the public about safe handling and display practices. This information helped collectors understand how to enjoy their luminous treasures responsibly.
These advancements have transformed the landscape of uranium glass. Today, enthusiasts can safely display and handle these items, contributing to a thriving market for unique collectibles.
The Cold War’s Influence on Production Processes
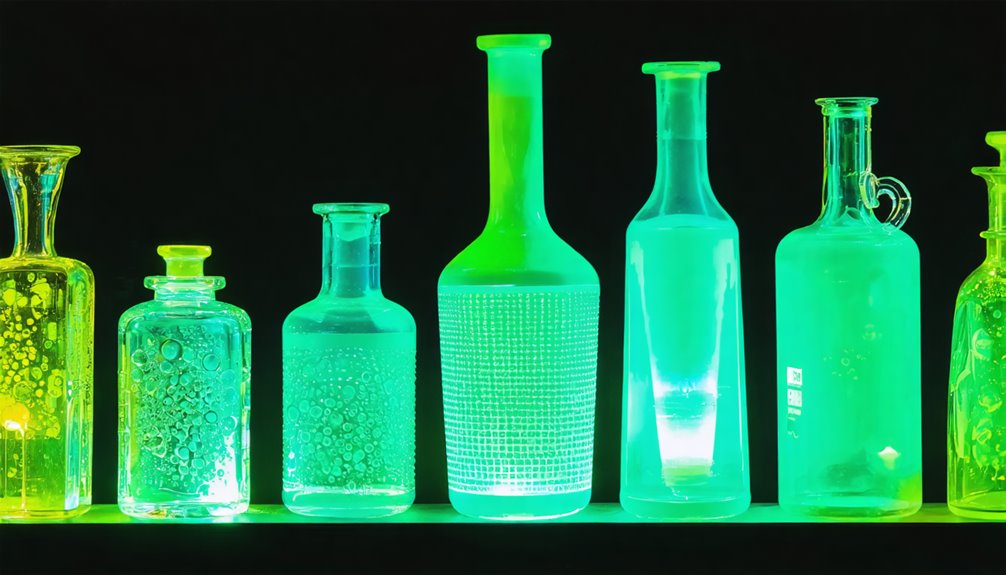
Uranium was a vital resource during the Cold War. Its supply for glassmakers decreased sharply as governments prioritized it for nuclear weapons and energy production. The U.S. government seized uranium during World War II for the Manhattan Project. This action halted uranium glass manufacturing in the U.S. This disruption continued into the Cold War.
Cold War demands for uranium disrupted glassmaking, as governments redirected supplies toward nuclear weapons and energy, halting uranium glass production.
By the 1950s, the nuclear industry controlled most uranium supplies. Glassmakers had to find alternative materials due to severe shortages. With uranium tightly regulated and redirected toward military uses, the once-thriving practice of uranium glassmaking diminished significantly.
This scarcity didn’t just limit production; it changed how glassmakers operated. They’d to innovate and adapt their techniques to survive in a competitive market.
The Cold War reshaped the landscape of glass manufacturing. Craftsmen turned to new materials and methods. In this challenging environment, creativity became essential. The art of making uranium glass, once popular, became a relic of the past.
Modern Safety Regulations and Manufacturing Standards
Uranium glass has an interesting history. It became popular in the late 19th century. At that time, glassmakers added uranium to their glass to create a vibrant green or yellow color. This unique glass was often used for decorative items and tableware.
In the early days, there were few safety measures in place. People enjoyed the beauty of uranium glass without considering potential risks. Over time, scientists discovered that uranium is radioactive. This led to concerns about safety and health.
Now, the manufacturing of uranium glass has returned, but with significant changes. Modern safety regulations ensure that the uranium content is kept below 0.1%. This protects consumers and meets health standards. To operate safely in this industry, manufacturers must take several steps.
First, they regularly check radiation levels with Geiger counters. This helps them monitor any potential risks.
Second, they follow guidelines from organizations like the EPA and OSHA. These regulations provide safe handling procedures.
Third, sourcing uranium must be transparent. Manufacturers need to verify where their uranium comes from.
Lastly, rigorous product testing is essential. This ensures that all products comply with safety standards before reaching consumers.
This careful approach promotes public safety. It also helps the industry thrive in a responsible way. The development of manufacturing techniques has come a long way from its origins. Today, it combines artistry with safety.
Contemporary Artistic Applications and Techniques
Uranium glass has a rich history that dates back to the early 19th century. Glassmakers discovered that adding uranium compounds to glass could create a vibrant green or yellow hue. This technique gained popularity in the Victorian era, with artisans crafting decorative items that captivated buyers. The glass not only looked beautiful but also glowed under ultraviolet light, adding an exciting visual element.
Over the years, manufacturing techniques for uranium glass evolved. Early glassmakers relied on simple methods for melting and molding. As technology advanced, they developed more sophisticated processes. These innovations allowed for finer details and more intricate designs. Today’s glassmakers can create elaborate patterns and shapes that weren’t possible in the past.
Notable manufacturers like Fenton and Mosser are reviving this art form. They experiment with various colors and styles, appealing to both collectors and newcomers. The luminous quality of uranium glass continues to attract interest. Artists are integrating this unique glass into mixed-media projects, combining it with other materials for striking visual contrasts.
Safety is a key concern when working with uranium glass. Modern artists understand the regulations regarding its use. They handle the material with care, ensuring their pieces are safe for public enjoyment. This awareness allows for creativity without compromising safety.
The blend of history, innovation, and safety makes uranium glass a fascinating subject in the world of contemporary art.
Scientific Research and Material Analysis Methods
Uranium glass has a fascinating history that intertwines with the development of manufacturing techniques. This unique glass, often called Vaseline glass, gained popularity in the late 19th and early 20th centuries. It was created by adding uranium oxide to glass during production, which resulted in its distinctive greenish-yellow hue and unique glow under ultraviolet light.
Uranium glass, or Vaseline glass, emerged in the late 1800s, captivating audiences with its glowing, distinctive greenish-yellow color under ultraviolet light.
The manufacturing process for uranium glass has evolved over time. Initially, glassmakers experimented with various materials to achieve vibrant colors. The introduction of uranium oxide not only enhanced the color but also provided a way to create glass that could fluoresce. This innovation marked a significant milestone in glass production.
Scientific methods have helped us uncover more about uranium glass. For example, micro-XRF scanning allows us to analyze the elemental makeup of the glass. These scans can identify the distribution of elements like aluminum, iron, and titanium, which may indicate manufacturing flaws or contamination from raw materials.
Elemental mapping reveals more than just composition. It offers insights into the production techniques used in different eras. For instance, the presence of copper oxide often suggests that glassmakers aimed for specific color effects, while sulfur might’ve been added to improve quality.
When it comes to uranium content, there’s a wide range. Some uranium glass samples contain as little as 0.191% uranium oxide, while others can have up to 25%. This variance reflects different manufacturing practices and the intended uses of the glass.
Radiation levels in uranium glass are another critical factor. Measurements show that these levels can be significantly higher than natural background radiation, sometimes reaching 150 times that amount. This aspect raises concerns about safety and regulation in the glass industry.
Sustainable Practices in Uranium Glass Production
Uranium glass has a fascinating past filled with creativity and scientific breakthroughs. The art of making this glass dates back to the early 19th century when artisans began using uranium compounds to create vibrant colors. These colorful pieces fascinated collectors and became popular in homes.
Over time, the methods for producing uranium glass evolved. Early glassmakers relied on traditional techniques, but advancements in manufacturing changed the game. Today, manufacturers focus on sustainability. They often use depleted uranium, which has lower levels of radioactivity. This shift helps reduce health risks and environmental concerns.
In modern production, eco-friendly materials play a vital role. Natural oxides and sustainable sources of silica are now common. This change reflects a commitment to environmental preservation. Recycling glass has also gained importance. It minimizes waste and significantly reduces the carbon footprint of new glass production.
Energy efficiency is another key aspect of today’s manufacturing practices. New melting equipment and techniques consume less energy, further promoting sustainability. As regulations become stricter, companies are vigilant in monitoring uranium levels in their products. This careful approach protects both consumers and the environment.
Frequently Asked Questions
How Did They Make Uranium Glass?
Uranium glass has an interesting history. It began in the early 19th century when glassmakers experimented with different materials. They discovered that adding uranium oxide to glass could create a unique color and fluorescence. This process involved combining silica, soda, and lime in specific amounts, along with uranium oxide.
The manufacturing techniques evolved over time. Glassmakers learned how to melt these components at high temperatures to create a smooth mixture. They used careful methods to ensure safety, as uranium, while interesting, can be hazardous if not handled properly. The result was vibrant, glowing glass that caught the eye of collectors and decorators.
During the 1920s and 1930s, uranium glass became quite popular. It was often used in household items like dishes and decorative pieces. People loved its bright green color and the way it glowed under ultraviolet light. Manufacturers refined their techniques, leading to a wider variety of products.
Today, uranium glass is valued by collectors, not only for its beauty but also for its historical significance. The development of manufacturing techniques allowed for the creation of this unique glass, making it a fascinating part of glassmaking history.
Why Is Uranium Glass Illegal?
Uranium glass, also known as Vaseline glass, has an interesting history. It emerged in the early 19th century when glassmakers discovered that adding uranium to glass could create vibrant colors and a unique glow under ultraviolet light. This technique allowed them to produce striking decorative items and tableware.
Manufacturing techniques evolved over the years. By the late 1800s, uranium glass became popular in households. Craftsmen used various methods, such as molding and blowing, to create beautiful, intricate designs. The glass was valued for its aesthetic appeal and novelty.
However, concerns about safety arose as the radioactivity of uranium was understood better. The potential health risks associated with exposure led to stricter regulations. While uranium glass is not entirely banned, its production and sale are closely monitored in many places. This is to protect public health and ensure the safety of consumers.
People still collect uranium glass today, appreciating its historical significance and unique properties. The glow of the glass under UV light continues to fascinate many enthusiasts. Understanding the balance between art and safety is crucial for those who admire this captivating material.
How to Tell if Uranium Glass Is Vintage?
Uranium glass has a fascinating history. It first appeared in the 1830s when glassmakers began experimenting with adding uranium oxide to glass. This unique material gives the glass its distinctive glow under ultraviolet light.
Manufacturing techniques evolved over the years. In the late 19th century, uranium glass became popular in the United States and Europe. Artisans crafted everything from elegant tableware to decorative pieces. The glowing quality caught the attention of collectors.
When you hold a piece of uranium glass, you might notice small bubbles or slight imperfections. These features are often signs of its age and craftsmanship. They help you determine if a piece is vintage or a modern reproduction.
Authentic uranium glass can enhance your collection. It’s important to learn about its history and how it was made. This knowledge empowers you to appreciate the artistry behind each piece.
What Year Did They Stop Making Uranium Glass?
Uranium glass has a fascinating history. Production began in the 1830s, but it really took off in the late 19th century. By the 1940s, widespread manufacturing had mostly stopped. The year 1942 marks a significant decline in production. This was mainly due to World War II and changes in consumer preferences.
After 1942, there were only a few limited revivals. Some producers brought it back in the 1950s and 1960s, but it never reached the same popularity. Understanding this timeline is crucial if you want to collect uranium glass. It helps you identify which pieces are truly vintage and valuable.
The manufacturing techniques evolved over the years, allowing for various designs and colors. Collectors often seek out unique shapes and patterns. Knowing the history and production timeline makes it easier to spot genuine items. So, if you’re on the lookout for collectible uranium glass, keep these historical facts in mind.
Conclusion
Uranium glass has a rich history, evolving from handmade pieces to modern industrial production. This glass, known for its unique green glow, reflects the creativity of its makers and the advancements in manufacturing techniques.
In the Victorian era, artisans crafted uranium glass with great care. Their work was marked by an appreciation for beauty and detail. During the Roaring Twenties, the focus shifted toward refinement and mass production, leading to new methods that allowed glassmakers to create more pieces efficiently.
Today, the production of uranium glass is guided by strict safety standards. Manufacturers prioritize both environmental sustainability and the health of their workers. This careful balance ensures that the glass remains both beautiful and safe for collectors and users alike.
Artists continue to explore traditional methods, blending age-old skills with modern science. This fusion leads to innovative designs and deeper understanding of how uranium glass interacts with light and heat. Researchers study its properties, revealing insights that benefit both art and science.
Overall, uranium glass’s glowing legacy captivates collectors and creators. Its history of craftsmanship and ongoing evolution in production techniques make it a fascinating subject for enthusiasts and experts alike.