How Radioactivity Influenced Manufacturing Techniques
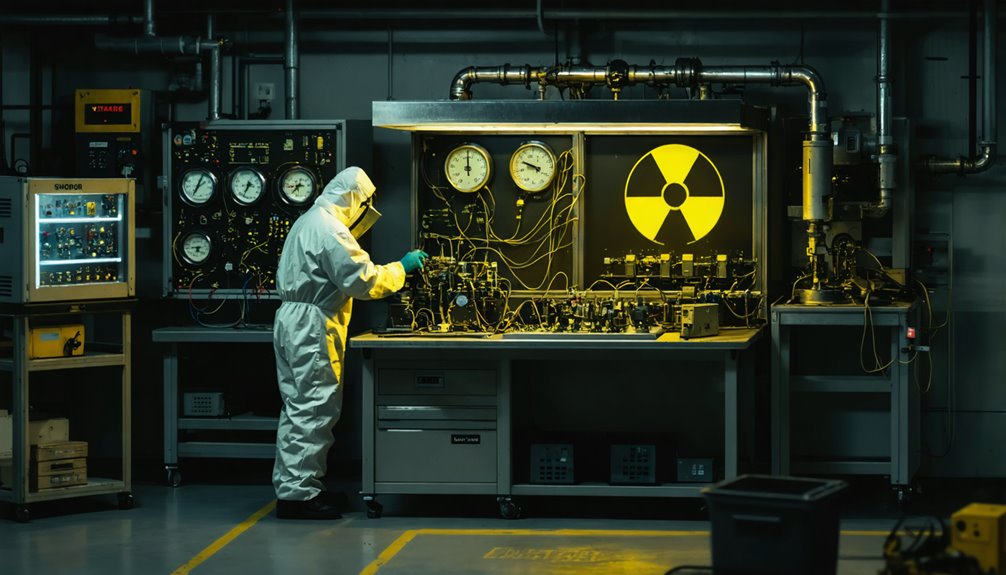
After the discovery of radioactivity, it had a significant impact on manufacturing techniques. One notable advancement was the introduction of precise, non-destructive testing methods like gamma radiography. This technique utilizes radioisotopes, specifically Cobalt-60 and Iridium-192, to find internal flaws in materials. With this innovation, industries such as aerospace and construction could perform safer and more accurate inspections.
Radioactivity also led to the creation of strict regulations governing the use of materials containing uranium. This was particularly relevant for products like uranium glass, which became popular for its unique glow and aesthetic appeal. Manufacturers had to balance the creative potential of using uranium with the need for safety measures to protect workers and consumers.
These changes represent just a portion of radioactivity’s broader influence on manufacturing. As we continue to explore this topic, we uncover more about how scientific discoveries shape industry practices and product development.
Key Takeaways
Radioactivity changed how things are made. Manufacturers had to follow stricter rules to handle radioactive materials safely. This shift led to new methods for testing materials, like gamma radiography. This technique helps check for defects without causing damage.
As awareness about radiation grew, companies changed their production processes. They focused on reducing the risks of radiation exposure. This change influenced the types of materials they chose and how they controlled quality.
Public safety was a major concern. Many industries decided to limit or stop using radioactive substances in products meant for consumers. This decision was important for gaining public trust.
Today, manufacturing has found ways to use radioactivity safely. For instance, additive manufacturing techniques are now used to create parts for nuclear reactors. This shows how the industry has evolved to balance innovation with safety.
Industrial Tracers: Enhancing Process Efficiency
When I first discovered uranium glass, I found it fascinating how this unique material has a rich history tied to the development of manufacturing techniques. Uranium glass, also known as Vaseline glass, contains small amounts of uranium, which gives it a distinct green or yellow hue. This glass became popular in the late 19th and early 20th centuries, especially during the Art Deco movement.
Discovering uranium glass revealed a captivating history intertwined with innovative manufacturing techniques, glowing subtly with its signature green or yellow hue.
Manufacturers used uranium to enhance the glass’s color and make it glow under ultraviolet light. This glow is due to the radioactivity of uranium, which, while minimal, adds an intriguing element to the glass. During this era, many artisans experimented with various compositions, leading to a wide range of styles and patterns. The production methods evolved, allowing for greater precision and creativity.
Uranium glass wasn’t just a novelty; it played a role in quality control. Glassmakers relied on the consistency of uranium’s properties to ensure their products met specific standards. As a result, it contributed to advancements in manufacturing processes that focused on uniformity and craftsmanship.
The demand for uranium glass declined after World War II due to changing tastes and safety concerns. However, collectors today appreciate its historical significance and unique characteristics.
The legacy of uranium glass reflects not only the ingenuity of its makers but also the ongoing evolution of manufacturing techniques in the glass industry.
Gauging Applications: Non-Contact Precision Measurement
When I first discovered uranium glass, I was amazed by its unique properties and colorful appearance. This glass, which contains uranium oxide, became popular in the early 20th century. Manufacturers used innovative techniques to create vibrant, glowing pieces. It wasn’t just a trend; it represented a significant advancement in glass-making.
The production of uranium glass involved careful blending of materials and precise heating methods. Craftsmen learned to manipulate the glass to achieve various shapes and colors. This creativity sparked a fascination for collectors and artists alike. It also led to the development of new manufacturing processes, which improved the overall quality of glass products.
However, as time passed, awareness grew about the radioactive properties of uranium glass. Regulations changed, impacting its production and use.
Today, collectors appreciate these pieces for their historical significance and artistic value. Understanding the journey of uranium glass gives insight into the evolution of manufacturing techniques and safety standards in the industry.
Industrial Process Leveling
Uranium glass, also known as Vaseline glass, has a fascinating history tied to the development of manufacturing techniques. In the late 19th century, glassmakers started to experiment with uranium dioxide, a compound that gives glass a distinctive greenish hue. This innovation allowed them to create unique and attractive pieces that glowed under ultraviolet light.
The introduction of uranium glass marked a significant advancement in glass manufacturing. Craftsmen could produce vibrant colors and interesting effects that captivated consumers. The glass wasn’t only beautiful but also functional, as it was often used for everyday items like tableware and decorative objects.
As manufacturing techniques evolved, the use of uranium glass expanded. Factories began to adopt more automated processes, which increased production speed and efficiency. This shift allowed glassmakers to meet growing consumer demand for these striking items. The combination of artistry and technology paved the way for a new era in glass manufacturing.
Despite its popularity, the use of uranium in glass raised safety concerns. Over time, regulations were put in place to limit exposure to radiation. Many consumers became more cautious, impacting the market for uranium glass. However, collectors still value these items for their historical significance and unique characteristics.
Today, the legacy of uranium glass continues to influence modern manufacturing techniques. The innovations from that era shaped how glass is produced and designed. Understanding the history of uranium glass offers insight into how creativity and technology can work together to enhance production methods.
Soil Density Assessment
Uranium glass has a fascinating history that changed manufacturing techniques. This unique glass contains uranium, which gives it a distinctive green or yellow hue. The glass became popular in the late 19th and early 20th centuries. It was often used in decorative items and tableware. The glowing effect of uranium glass under ultraviolet light added to its charm.
Manufacturers experimented with different methods to create uranium glass. They mixed silica sand with soda and uranium oxide. This combination led to a smooth, shiny finish. Craftsmen used molds to shape the glass, allowing for intricate designs.
As the demand grew, factories scaled up production. They adopted assembly line techniques, increasing efficiency and making uranium glass more accessible to the public.
Despite its beauty, uranium glass faced scrutiny due to its radioactive content. Safety concerns emerged, leading to regulations on its production and sale.
Yet, many people continued to appreciate its artistry and collectibility. Today, uranium glass is a sought-after item for collectors, showcasing the evolution of glass manufacturing and the balance between innovation and safety.
Radioisotopes in Quality Assurance and Inspection
Uranium glass, also known as Vaseline glass, has a fascinating history. It gained popularity in the 19th century, during the Victorian era. At that time, glassmakers discovered that adding uranium oxide to glass gave it a unique greenish-yellow hue and made it glow under ultraviolet light. This glow was a captivating feature that appealed to many collectors.
Manufacturers used uranium glass in various products, including tableware and decorative items. The process of creating this glass involved melting silica with uranium compounds, which produced distinctive pieces. As interest in uranium glass grew, production techniques evolved. Artisans experimented with different colors and patterns, leading to a wide array of artistic designs.
Uranium glass artisans innovated endlessly, experimenting with colors and patterns to create distinctive tableware and decorative pieces cherished by collectors.
However, the use of uranium in glassmaking raised safety concerns. By the mid-20th century, awareness of radioactivity increased. As a result, many manufacturers stopped using uranium in their products.
Today, uranium glass is primarily collected as a historical artifact rather than produced for everyday use. Despite its decline, uranium glass remains significant in the study of manufacturing techniques. It illustrates how innovation can lead to unique products, even while highlighting the importance of safety in production.
Collectors and historians continue to cherish these pieces, recognizing their place in the evolution of glassmaking.
Gamma Radiography: Detecting Internal Defects
When I think about the history of uranium glass, its unique charm captures my attention. This special type of glass, known for its bright green or yellow hue, gained popularity in the late 19th century. It was often used to create decorative items and tableware. The glow it emits under ultraviolet light makes it stand out in any collection.
The development of manufacturing techniques played a crucial role in the rise of uranium glass. Early glassmakers experimented with adding uranium oxide to their mixtures. This innovation allowed them to produce vibrant colors and achieve a striking appearance.
Over time, advancements in glassblowing and molding techniques improved the quality and consistency of the products.
In the early 20th century, uranium glass became a household favorite, especially during the Great Depression. It was affordable and accessible, making it popular among consumers. The introduction of mass production methods made it easier to create intricate designs and patterns, enhancing its appeal.
However, the use of uranium in glassmaking sparked safety concerns. As awareness grew about the potential health risks associated with uranium exposure, manufacturers faced pressure to change their practices.
By the mid-20th century, many companies shifted away from using uranium in glass production, leading to a decline in its popularity.
Today, collectors seek out uranium glass for its historical significance and aesthetic value. It serves as a reminder of the past and the evolution of manufacturing techniques in the glass industry. The legacy of uranium glass continues to intrigue enthusiasts and historians alike.
Inspecting Weld Integrity
One interesting method to inspect weld integrity is gamma radiography. This non-destructive testing technique uses gamma rays to look inside metal parts and find hidden issues. It works by using isotopes like Cobalt-60 or Iridium-192 to emit radiation. This radiation penetrates welded joints, revealing internal defects like cracks, voids, and inclusions. These flaws can weaken structures. In industries like aerospace and construction, knowing that parts are reliable is essential. That’s why powerful inspection methods are important. They help ensure accuracy without slowing down production.
To use gamma radiography well, I focus on a few key points. First, I ensure proper shielding is in place. This keeps personnel safe from radiation exposure. Second, I monitor the inspection process continuously. This enhances safety. Finally, I aim to minimize disruptions in manufacturing. Keeping productivity high is crucial for industry operations.
Interestingly, the development of gamma radiography reflects advancements in manufacturing techniques. As industries grew, the need for reliable inspection methods became clear. The ability to find flaws without harming the material was a game-changer.
It paved the way for safer and more efficient production processes. This evolution shows how technology can improve quality and safety in manufacturing.
Non-Destructive Testing Benefits
Uranium glass, also known as Vaseline glass, has a fascinating history tied to the development of manufacturing techniques. Originating in the early 19th century, this distinctive glassware contains small amounts of uranium oxide, which gives it a unique greenish hue and allows it to glow under ultraviolet light.
The process of creating uranium glass was innovative for its time. Glassmakers experimented with various materials to achieve different colors and effects. Adding uranium was a breakthrough that not only enhanced the aesthetic appeal but also improved the glass’s durability. This technique was widely embraced, especially in the United States and Europe, where it became particularly popular during the Victorian era.
Manufacturers utilized uranium glass for everyday items like tableware and decorative pieces. The use of uranium also reflected the era’s fascination with science and technology. People were drawn to the novelty of these glowing objects, which became a symbol of modernity.
As concerns about radiation safety grew, the popularity of uranium glass waned. However, it remains a collectible today, admired for its unique characteristics and historical significance.
The story of uranium glass illustrates how advancements in manufacturing techniques can create items that capture the public’s imagination, even as societal attitudes evolve.
Industrial Safety Enhancement
Uranium glass, often called Vaseline glass, has a fascinating history rooted in the development of manufacturing techniques. This unique glass contains small amounts of uranium, giving it a distinctive green or yellow hue and a glow under ultraviolet light. The use of uranium in glassmaking started in the early 19th century. Manufacturers discovered that adding uranium oxide to glass not only enhanced its color but also improved its clarity.
During the Victorian era, uranium glass became popular in households. People admired its beauty and the way it shone in the light. Factories began producing various items, from decorative pieces to practical tableware. The manufacturing process allowed for intricate designs, making these items desirable among collectors.
As time went on, the safety and perception of uranium glass shifted. By the mid-20th century, the awareness of radiation hazards increased. Despite concerns, many collectors still appreciate uranium glass for its unique qualities. They enjoy how it adds a touch of history to their collections.
Today, the manufacturing of uranium glass has largely stopped. However, the legacy of its production techniques remains. The glass serves as a reminder of how innovation can lead to both beauty and caution in industrial practices.
Collectors often seek out these pieces, valuing both their aesthetic appeal and the story behind their creation.
Neutron Radiography: Advanced Analytical Techniques

Uranium glass, also known as Vaseline glass, has a fascinating history tied to the development of manufacturing techniques. This unique glass contains uranium oxide, which gives it a distinctive green or yellow hue. The production of uranium glass began in the early 19th century. Manufacturers used uranium to enhance the glass’s color and make it fluoresce under ultraviolet light.
During the late 1800s, uranium glass gained popularity. Craftsmen appreciated its aesthetic qualities and its ability to catch the eye of consumers. The glass was often used for decorative items, such as vases and tableware. Its appeal grew with the rise of Art Deco in the 1920s, when bold colors and unique designs became fashionable.
In the mid-20th century, concerns about radiation emerged. Although the levels of radiation in uranium glass are low and generally considered safe, this led to a decline in its use. Manufacturers began to explore safer alternatives, shifting away from uranium in glass production.
Today, collectors value uranium glass for its historical significance and unique characteristics. It serves as a reminder of how manufacturing techniques evolve in response to both consumer demand and safety considerations.
The legacy of uranium glass highlights the delicate balance between innovation and responsibility in the world of manufacturing.
Carbon Dating in Manufacturing: Material Age Assessment
When looking at the history of uranium glass, it’s fascinating to see how manufacturing techniques have evolved. Uranium glass, known for its vibrant green or yellow hue and its unique ability to fluoresce under UV light, dates back to the early 19th century. The use of uranium in glassmaking began when manufacturers discovered that adding uranium compounds to glass created beautiful and striking colors.
This glass gained popularity in the 1920s and 1930s. Manufacturers used uranium to enhance the visual appeal of their products. It was a time when decorative glassware became a staple in many households. Collectors today appreciate these pieces not just for their beauty, but also for the history they represent.
As I explore these artifacts, I consider their age and authenticity. Just like carbon dating helps assess the age of wood or textiles, scientists can analyze uranium glass to understand its origins. By studying the composition and production methods, experts can confirm when and where these items were made.
This process is crucial for collectors and historians. It assures them that their pieces are genuine and helps to establish their value.
In the world of manufacturing, the evolution of techniques and materials like uranium glass showcases the creativity and innovation of the past. Understanding this history enriches our appreciation of glassware today.
Historical Material Verification
The history of uranium glass is fascinating. This unique glass, often called Vaseline glass, contains a small amount of uranium, which gives it a distinctive green or yellow hue and makes it glow under ultraviolet light. The manufacturing of uranium glass began in the 1830s and gained popularity during the Victorian era.
Uranium glass was initially created for its aesthetic appeal. It was used in various household items, such as dishes and decorative pieces. The incorporation of uranium into glassmaking emerged as a new technique. This innovation allowed manufacturers to produce vibrant colors and unique designs that captured the public’s imagination.
The use of uranium in glass faced scrutiny over the years due to health concerns. However, the levels of uranium in the glass are typically low and considered safe for display. This historical context is crucial for understanding the development of manufacturing techniques in glassmaking.
Today, uranium glass is valued by collectors and historians alike. It represents not only a unique material but also a chapter in the story of industrial innovation. The study of this glass helps us appreciate the evolution of manufacturing practices and the creativity of artisans in the past.
Authenticity Through Isotope Analysis
Uranium glass, also known as Vaseline glass, is a fascinating material with a rich history. Its distinct green or yellow tint comes from the addition of uranium oxide during the manufacturing process. This unique glass first became popular in the 1830s and continued to be made until the mid-20th century.
The manufacturing techniques for uranium glass evolved over the years. Early glassmakers experimented with various formulas, seeking to enhance the glass’s clarity and color. The use of uranium not only provided a striking appearance but also allowed for the creation of striking fluorescence under ultraviolet light. This feature made uranium glass particularly appealing to collectors and those seeking decorative items.
As the demand for uranium glass grew, manufacturers began to refine their techniques. They learned how to manipulate the ratios of uranium to other materials, resulting in glass that varied in color and opacity. This experimentation led to a wide range of products, from tableware to art pieces, showcasing the creativity of the era.
Over time, the perception of uranium glass changed. Initially celebrated for its beauty and novelty, it later faced scrutiny due to concerns about radiation exposure. Despite this, many collectors appreciate uranium glass for its historical significance and unique characteristics.
Naturally-Occurring Radioisotopes: Industrial Applications
Uranium glass, often referred to as Vaseline glass, has a fascinating history tied to the development of manufacturing techniques. This unique glass contains small amounts of uranium, which gives it a distinctive green or yellow hue and makes it glow under ultraviolet light.
The use of uranium in glass dates back to the 1830s. Early manufacturers discovered that adding uranium to glass enhanced its clarity and brilliance. This was especially popular in the 19th century when glassware became a symbol of luxury. Skilled artisans used innovative methods to create intricate designs and patterns, making these pieces highly sought after.
As technology advanced, so did the manufacturing processes. The introduction of industrial machines allowed for mass production of uranium glass. This significantly reduced costs and made the glassware accessible to a broader audience. The glowing effect of uranium glass became a novelty, attracting collectors and enthusiasts.
However, the use of uranium in glass also raised safety concerns. By the mid-20th century, regulations began to form around the use of radioactive materials in consumer products. Manufacturers had to ensure that the levels of uranium were within safe limits. This led to more stringent quality controls and the development of safer alternatives.
Today, uranium glass is appreciated for its historical value and aesthetic appeal. Collectors often seek out vintage pieces, and some modern artisans continue to experiment with uranium glass while adhering to safety guidelines.
The journey of uranium glass reflects the evolution of manufacturing techniques and the balance between innovation and safety.
Artificially-Produced Radioisotopes: Expanding Industrial Uses
Uranium glass, also known as Vaseline glass, has a fascinating history tied to the development of manufacturing techniques. This unique glass contains small amounts of uranium, which gives it a distinctive greenish hue and makes it glow under ultraviolet light. The use of uranium in glass dates back to the mid-19th century, during a time when glassmakers sought to create vibrant, eye-catching products.
Initially, glassmakers discovered that adding uranium oxide to glass could produce a striking color. This innovation led to the production of decorative items, such as vases and tableware. The glowing effect of uranium glass captured the imagination of consumers and collectors alike.
As techniques advanced, manufacturers learned how to manipulate the amount of uranium used, allowing for a range of colors and effects. The popularity of uranium glass surged in the early 20th century, especially during the Art Deco movement. Mass production techniques were refined, enabling factories to create these beautiful items at scale.
People were drawn to the novelty of glowing glass, and it became a staple in many households. However, the use of uranium in glass declined after World War II due to rising concerns about radiation exposure. Regulations changed, and the public became more aware of the potential risks.
As a result, manufacturers shifted their focus to other materials, moving away from uranium glass. Today, uranium glass is considered a collectible item. Enthusiasts appreciate its historical significance and unique properties.
While it may no longer be produced in large quantities, its legacy endures as a testament to the creativity and innovation of glassmakers throughout history.
Radiotracers for Process Monitoring
Uranium glass has a fascinating history rooted in the development of manufacturing techniques. This type of glass, also known as Vaseline glass, contains small amounts of uranium oxide, giving it a distinctive green or yellow hue. It became popular in the late 19th century and was widely produced until the mid-20th century.
The process of creating uranium glass involved melting silica sand, soda, and uranium oxide at high temperatures. This mixture resulted in a glass that not only looked unique but also had a slight radioactivity. The uranium added an appealing glow under ultraviolet light, which captivated many collectors and enthusiasts.
Factories used innovative methods to shape and mold the glass, allowing for intricate designs and patterns. During its peak production period, uranium glass was used for various household items such as bowls, cups, and decorative pieces. The glass was affordable and accessible, making it a favorite among the middle class.
However, after World War II, concerns about radiation safety led to a decline in its popularity. Manufacturers shifted to other materials, and production of uranium glass decreased significantly.
Today, uranium glass is considered a collectible item. Many people appreciate its historical significance and unique aesthetic. Collectors often seek out pieces from the early 20th century, showcasing the craftsmanship of that era. The revival of interest in vintage items has sparked a renewed fascination with uranium glass, highlighting its place in the history of manufacturing techniques.
Gamma Radiography in Inspection
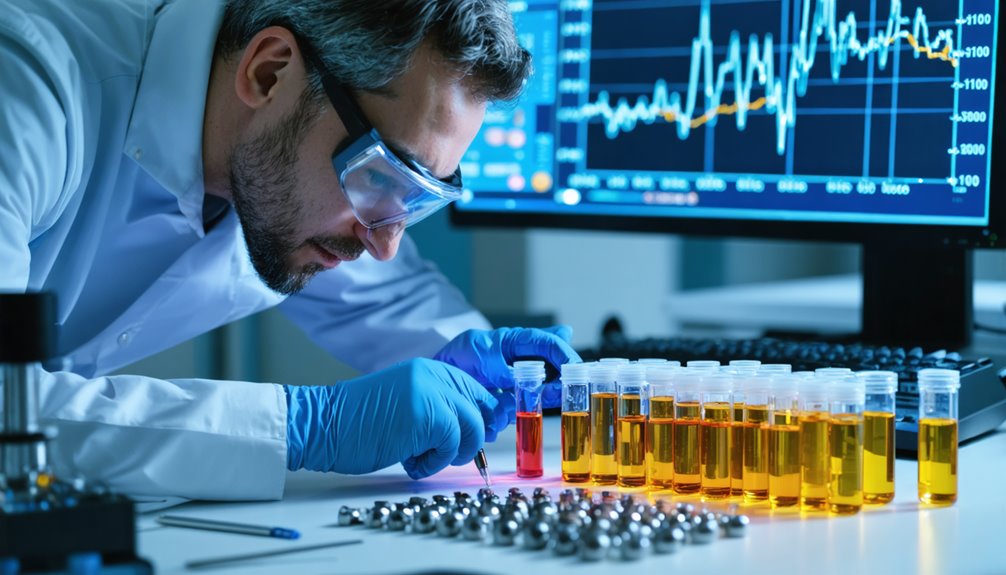
Uranium glass, also known as Vaseline glass, has a fascinating history tied to the development of manufacturing techniques. This unique glass contains small amounts of uranium, which gives it a distinctive green or yellow hue and allows it to fluoresce under ultraviolet light.
In the late 19th century, glassmakers began experimenting with uranium as a coloring agent. They found that adding uranium oxide not only enhanced the color but also made the glass more appealing to collectors. This period marked a significant advancement in glass manufacturing. Techniques improved, and artisans developed new methods to create intricate designs and patterns.
During the early 20th century, uranium glass became especially popular in the United States. It was widely used for tableware and decorative items. The manufacturing process involved melting silica sand, soda ash, and uranium oxide together, then shaping the molten glass into various forms.
This era saw a rise in household items made from uranium glass, as it was both beautiful and functional. The use of uranium in glassmaking continued until the mid-20th century when concerns about radiation safety emerged. Manufacturers had to adapt their techniques and materials to comply with new regulations.
Despite this shift, many collectors still value uranium glass for its historical significance and vibrant appearance. Today, uranium glass serves as a reminder of the evolution of manufacturing techniques and the interplay between creativity and safety. Collectors and enthusiasts appreciate its unique properties, ensuring that the legacy of this captivating glass endures.
Gauging With Radioisotope Instruments
Uranium glass, known for its striking green hue, has a fascinating history tied to the development of manufacturing techniques. In the late 19th century, glassmakers began experimenting with uranium oxide, a byproduct of uranium mining. This innovation led to the creation of a unique type of glass that not only glowed under ultraviolet light but also showcased vibrant colors.
The manufacturing process for uranium glass evolved over time. Early artisans used traditional glass-blowing methods, but advancements in technology allowed for more precise production techniques. As the 20th century progressed, mass production of uranium glass became feasible, making it accessible to a broader audience.
Factories employed automated machinery, improving efficiency and consistency in the finished product. Uranium glass found various applications beyond decorative items. It was used in scientific instruments and even in some household items.
However, the use of uranium in glass faced scrutiny due to safety concerns over radioactivity. By the mid-20th century, manufacturers began to phase out uranium in glassmaking, favoring safer alternatives.
Despite its decline in production, uranium glass remains a topic of interest for collectors and historians. The unique properties of this glass, along with its vibrant appearance, continue to captivate those who appreciate its historical significance and artistic value.
Radiation Safety and Regulatory Compliance in Industry
Uranium glass has a fascinating history that reflects the evolution of manufacturing techniques. This unique glass, often called Vaseline glass, emerged in the early 19th century. Manufacturers discovered that adding uranium oxide to glass created a vibrant green or yellow hue. This addition also gave the glass a captivating glow under ultraviolet light.
As demand grew, factories found innovative ways to produce uranium glass in large quantities. The manufacturing process became more efficient, allowing for the creation of various decorative items. Bowls, vases, and even tableware became popular, showcasing the glass’s striking appearance.
In the 20th century, uranium glass gained notoriety due to its radioactivity. Although the levels of radiation are generally low and not harmful, safety concerns arose. Regulations were put in place to ensure that manufacturers adhered to safety standards. This shift in focus highlighted the need for responsible production methods.
Today, uranium glass is collected by enthusiasts and appreciated for its beauty and historical significance. The techniques used in its production have evolved, reflecting advances in glassmaking and an increased awareness of safety. As we enjoy these pieces, we also recognize the importance of understanding the materials and methods that brought them to life.
Process Optimization Through Radiometric Control
Uranium glass, also known as Vaseline glass, has a fascinating history that reflects the evolution of manufacturing techniques. This unique glass contains small amounts of uranium, which gives it a distinctive green or yellow hue and allows it to fluoresce under ultraviolet light.
The production of uranium glass began in the 1830s. Manufacturers experimented with adding uranium oxide to glass mixtures, discovering that it not only enhanced the color but also improved the glass’s clarity and brilliance. The technique quickly caught on, with glassmakers in Europe and the United States incorporating uranium into their products.
During the late 19th and early 20th centuries, uranium glass became popular for household items like tableware and decorative pieces. The glass was often used for its aesthetic qualities, but it also had practical benefits. The inclusion of uranium made the glass more durable and resistant to breaking.
World War II sparked a surge in uranium glass production. The need for uranium for nuclear weapons led to a boom in uranium mining and processing. As a result, glass manufacturers had better access to uranium, and they produced more items than ever before.
However, after the war, concerns about radiation safety began to rise. In the 1970s, the popularity of uranium glass declined as awareness of health risks associated with radiation grew. Many manufacturers stopped using uranium in their glass products.
Today, collectors appreciate uranium glass for its historical significance and unique properties.
Environmental Monitoring Using Radioactive Isotopes
Uranium glass has a fascinating history that dates back to the 1830s. Early glassmakers experimented with different materials to create unique colors and effects. They discovered that adding uranium oxide to glass produced a striking green or yellow hue. This wasn’t just for aesthetics; it also made the glass glow under ultraviolet light.
Manufacturing techniques evolved over the years. Initially, uranium glass was handmade by artisans. They carefully mixed the ingredients and shaped the glass by hand. As demand grew, factories began to adopt new methods. They developed more efficient ways to mix and melt glass, which allowed for mass production. This made uranium glass more accessible to the public.
During the late 19th and early 20th centuries, uranium glass became popular for household items. People loved the vibrant colors and the novelty of the glow. Items like vases, dishes, and decorative pieces were widely produced. However, the use of uranium in glassmaking raised safety concerns.
In the 1940s, concerns about radiation exposure led to stricter regulations. Manufacturing techniques had to be adjusted to ensure safety. Some glassmakers stopped using uranium altogether, while others found ways to reduce the risks.
Today, uranium glass is mostly collected by enthusiasts and valued for its historical significance.
Understanding the development of manufacturing techniques in uranium glass gives us insight into both the creativity and the challenges faced by glassmakers. It shows how art and science can come together, leading to beautiful and intriguing objects that tell a story of innovation and caution.
Radioactivity in Additive Manufacturing: Advancing Nuclear Applications
Uranium glass is a fascinating part of manufacturing history. It shows how radioactive materials shaped traditional methods.
Today, we see radioactivity in a new light with advanced techniques like additive manufacturing (AM). This modern approach lets us create nuclear reactor parts that can withstand harsh neutron radiation. These parts maintain their strength and flexibility, which is crucial for safe reactor operation.
Collaborating with organizations such as the Nuclear Science and Engineering Center (NuSEC) boosts our efforts. They help us evaluate the durability of AM components under tough reactor conditions.
At the Idaho National Laboratory, the Advanced Test Reactor plays a significant role. It allows researchers to expose AM samples to radiation, providing essential performance data. This data helps us ensure safety and reliability in nuclear applications.
Additive manufacturing allows us to design complex shapes that traditional methods can’t achieve. This capability leads to cost savings and reduced downtime when replacing old reactor components.
Moreover, it improves reactor efficiency by refining component designs. Overall, the development of manufacturing techniques like AM is setting a new standard in the nuclear industry.
Non-Destructive Testing for Critical Infrastructure
Uranium glass, also known as Vaseline glass, has a fascinating history linked to the development of manufacturing techniques. This unique glass, which contains small amounts of uranium, first appeared in the early 19th century. Initially, glassmakers used uranium to create vibrant green and yellow hues, adding a distinctive touch to their products. The glass glows under ultraviolet light due to the uranium content, which has made it popular among collectors.
The production of uranium glass grew alongside advancements in glass-making technology. As techniques evolved, artisans learned to manipulate the glass more skillfully, enhancing its aesthetic appeal. By the late 19th century, uranium glass was widely produced, especially in the United States and Europe. Factories developed effective methods to incorporate uranium into glass mixtures, resulting in a variety of decorative items, including dishes, vases, and beads.
However, the use of uranium raised concerns over safety due to its radioactive properties. Despite this, the glass remained in production until the mid-20th century when public awareness of radiation hazards increased. Manufacturers began to phase out uranium from their products, leading to a decline in uranium glass production.
Today, uranium glass is a sought-after collectible. It serves as a reminder of how manufacturing techniques have evolved over time, reflecting changing attitudes toward materials and safety. Collectors appreciate its unique qualities, and many enjoy showcasing these colorful pieces that tell a story of innovation and change in the glass industry.
Future Developments in Radioisotope-Driven Manufacturing Techniques
Uranium glass, also known as Vaseline glass, has a fascinating history tied to the development of manufacturing techniques. It gained popularity in the 19th century when glassmakers discovered that adding uranium oxide to glass could enhance its color and fluorescence. This unique property made uranium glass a favorite for decorative items and tableware, captivating many collectors.
Uranium glass captivated 19th-century collectors with its vibrant colors and glowing fluorescence, reflecting innovative advancements in glassmaking techniques.
The production of uranium glass involved blending silica, soda, and uranium oxide. This process required skilled artisans who mastered the art of glassblowing and molding. The result was vibrant green or yellow glass that glowed under ultraviolet light. Manufacturers used these techniques to create intricate designs, often featuring patterns that showcased the glass’s luminescent qualities.
During the early 20th century, the use of uranium in glassmaking peaked. The demand for uranium glass surged, particularly in the United States, where it was marketed for its aesthetic appeal. However, as awareness of the health risks associated with radioactive materials grew, the popularity of uranium glass began to decline.
Today, enthusiasts appreciate uranium glass for its historical significance and unique characteristics. Collectors often seek out rare pieces, and some artists have even revived the technique, blending traditional glassmaking with modern designs.
The legacy of uranium glass continues to influence contemporary manufacturing methods and materials, highlighting the ongoing evolution of industrial processes.
Frequently Asked Questions
How Is Radioactivity Used in the Industry?
Uranium glass, also known as Vaseline glass, has an interesting history that dates back to the early 19th century. Manufacturers discovered that adding uranium to glass gave it a vibrant green or yellow color. This unique glass became popular for decorative items and tableware.
In the late 1800s, uranium glass emerged as a fashionable choice for both everyday use and artistic pieces. It was made using a combination of silica, soda, and uranium oxide. The uranium added not only color but also made the glass fluorescent under ultraviolet light. This captivating feature drew attention and made uranium glass a favorite among collectors.
The manufacturing techniques for uranium glass evolved over time. Early glassmakers relied on traditional methods, but as industrial processes advanced, production became more efficient. Factories began to use molds, allowing for consistent shapes and sizes. This shift made uranium glass more accessible to the general public.
During the mid-20th century, the popularity of uranium glass peaked. It was widely produced in the United States and Europe. However, concerns about the safety of uranium led to a decline in its use. By the end of the 20th century, many manufacturers stopped using uranium in glass production altogether.
Today, uranium glass is mainly collected by enthusiasts. Its unique properties and historical significance keep it alive in the world of antiques. The story of uranium glass reflects the broader changes in manufacturing techniques and consumer preferences over the years.
What Are 5 Uses of Radiation in Industry?
Uranium glass, also known as Vaseline glass, has a fascinating history tied to the development of manufacturing techniques. This unique glass contains small amounts of uranium, giving it a distinctive green or yellow hue and allowing it to fluoresce under ultraviolet light.
In the 19th century, glassmakers started experimenting with various materials to enhance their products. The inclusion of uranium was not initially for its radioactive properties. Instead, it was valued for its ability to create vibrant colors and improve the clarity of glass. During this period, the industrial revolution was in full swing, leading to advancements in glass production methods.
Manufacturers used uranium glass to create decorative items like vases, bowls, and tableware. These pieces became popular among consumers for their eye-catching appearance. As techniques improved, the glass became more accessible, and production increased.
In the early 20th century, uranium glass reached its peak popularity. Many households owned pieces made from this striking material. However, as awareness of radiation grew, the use of uranium in glass declined. By the mid-20th century, many manufacturers stopped using uranium, shifting towards safer materials.
Today, uranium glass is considered a collectible item. Enthusiasts appreciate its unique qualities and historical significance. The development of manufacturing techniques played a crucial role in the rise and fall of uranium glass, showcasing the balance between innovation and safety in industry.
Is Radiation Used in Manufacturing?
Uranium glass, also known as Vaseline glass, has a unique history in manufacturing. This glass contains small amounts of uranium, which give it a distinctive green or yellow color and make it glow under ultraviolet light. The use of uranium in glassmaking began in the late 19th century. At that time, manufacturers sought new ways to enhance the aesthetic appeal of their products.
The production of uranium glass gained popularity during the Art Deco period in the 1920s and 1930s. Many companies, like Fenton and Westmoreland, produced striking pieces that captivated consumers. The glass was not only beautiful but also functional, often used for tableware and decorative items.
Despite its charm, the use of uranium in glass has raised safety concerns. The radiation levels in uranium glass are low, but awareness of potential hazards has led to changes in manufacturing practices. Today, many manufacturers avoid using uranium due to safety regulations and public concern.
What Are Three Ways That Radioactivity Is Being Used in Medical Technology?
Radioactivity plays a significant role in modern medical technology. One key application is Nuclear Imaging. This technique uses small amounts of radioactive materials to create images of the inside of the body. Doctors can see how organs and tissues function, helping them diagnose various conditions.
Another important use is targeted radiotherapy. This method focuses radiation directly on cancerous cells. The goal is to destroy these harmful cells while minimizing damage to surrounding healthy tissue. It’s a vital treatment that can improve outcomes for patients with cancer.
Brachytherapy is also a noteworthy application of radioactivity in medicine. This technique involves placing radioactive sources inside or very close to tumors. It precisely delivers radiation, which can effectively shrink tumors while preserving the healthy areas around them. This method is particularly beneficial for certain types of cancers.
Conclusion
Uranium glass has a fascinating history tied to the development of manufacturing techniques. This unique glass, which contains small amounts of uranium, became popular in the late 19th and early 20th centuries. Manufacturers discovered that adding uranium to glass could enhance its color and fluorescence. The result was a vibrant green or yellow glass that glowed under ultraviolet light.
During this period, glassmakers experimented with different compositions to create decorative items and tableware. The use of uranium not only added beauty but also made the glass more durable. This innovation was significant, as it represented a blend of artistry and science in manufacturing.
As World War II approached, the demand for uranium increased for military purposes. Some manufacturers shifted their focus to producing items that would support the war effort. After the war, uranium glass experienced a resurgence in popularity, as many people were fascinated by its unique properties.
However, the use of uranium in glass also raised health concerns. Over time, regulations changed, and the production of uranium glass became limited. Today, collectors appreciate these pieces as historical artifacts that represent a unique intersection of chemistry and craftsmanship.
Overall, the story of uranium glass highlights how manufacturing techniques can evolve through experimentation and innovation. It shows how materials can be transformed into something beautiful and functional while also reflecting the social and scientific context of the time.