The Revival of Traditional Techniques in Modern Uranium Glassmaking
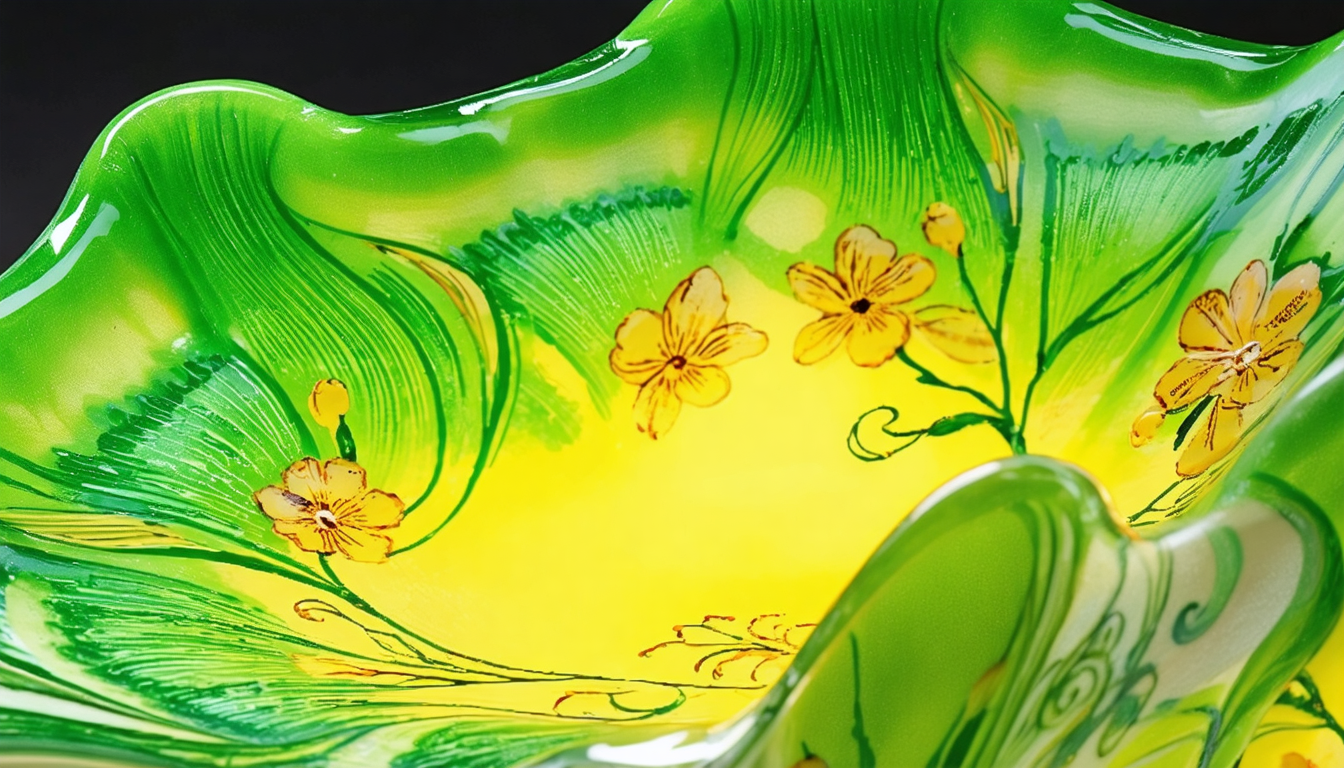
Uranium glass has a rich history that dates back to the early 19th century. Initially, glassmakers added uranium oxide to glass to create a vibrant green color. This unique material became popular in the Victorian era, where it was used for decorative items and tableware. The glow of uranium glass under ultraviolet light fascinated many.
The techniques for making uranium glass have evolved over the years. Artisans today combine traditional methods with modern safety standards. They use hand-blowing techniques to shape the glass, which gives each piece a unique personality. The glass is often adorned with intricate, hand-painted designs. After painting, the pieces are kiln-fired. This process ensures that the designs remain intact and vibrant.
Gold leaf accents are sometimes added to enhance the beauty of the glass. These accents catch the light beautifully and increase the fluorescence when exposed to UV light. Collectors of vintage and historically styled pieces have sparked renewed interest in this craft. Many appreciate the connection to the past and the artistry involved in creating each item.
There is still much to learn about uranium glass and its production. As artisans continue to explore new techniques and materials, the craft remains alive and well. The balance of historical tradition and modern innovation keeps uranium glassmaking relevant. It is a testament to the enduring appeal of this fascinating craft.
Key Takeaways
Uranium glass, known for its striking green glow, has a fascinating history. Originally made in the 19th century, it became popular for its unique aesthetic and believed health benefits. Over time, mass production took over, leading to less emphasis on craftsmanship.
Recently, there has been a resurgence in traditional glassmaking techniques. Artisans are hand-blowing uranium glass, producing distinctive pieces that stand out from mass-produced items. This method allows for greater creativity and individuality in each creation.
Moreover, skilled artisans are reviving hand-painting and kiln-firing methods. These techniques add intricate designs, giving a sense of depth and historical authenticity to modern uranium glass. Such attention to detail sets these pieces apart from their industrial counterparts.
Gold leaf embellishments are also making a comeback. When artisans apply gold leaf, it enhances the natural fluorescence of uranium glass, making each piece visually striking. This decorative technique adds a luxurious touch that appeals to collectors.
Collector interest is on the rise. Many enthusiasts are drawn to the historical aspects of uranium glass. This demand has encouraged artisans to adopt historically accurate methods. As a result, limited-run collaborations and custom designs have emerged, reflecting a blend of tradition and modern taste.
Sustainability is becoming important too. Many artisans are using recycled materials and energy-efficient methods in their glassmaking. This approach not only respects the environment but also aligns with the revival of traditional techniques.
Overall, the development of manufacturing techniques in uranium glassmaking highlights a blend of history, artistry, and sustainability. It shows how the past can inspire the present, leading to beautiful, one-of-a-kind pieces.
Historical Foundations of Uranium Glass Techniques
In the early 1800s, Bohemian glassmakers made a significant breakthrough. They added uranium dioxide to glass mixtures, creating stunning colors. This invention, uranium glass, quickly captured attention throughout Europe. In Victorian England, it represented the marvels of science and the spirit of the industrial revolution.
By the 1830s, French factories, such as Choisy-le-Roi, began producing uranium glass known for its unique glow. Under ultraviolet light, these pieces sparkled with a bright fluorescence. People were fascinated by this decorative glassware, which became a popular choice in homes and exhibitions.
From the 1880s to the 1920s, the demand for luminous uranium glass soared. This period marked its peak and solidified its place in history. However, interest waned in the following decades.
Fortunately, traditional uranium glassmaking techniques have seen a revival in recent years. Today, skilled artisans are reconnecting with the craft of their 19th-century counterparts. They blend historical methods with modern safety practices. This revival highlights the beauty and complexity of uranium glass, ensuring its legacy continues to shine brightly.
Hand-Blowing: Mastery Revived in Modern Uranium Glassmaking
Uranium glass has a rich history that dates back to the early 19th century. This unique glassware, known for its striking green or yellow color and its ability to fluoresce under UV light, became popular during the Victorian era. Craftsmen discovered that adding uranium oxide to glass could produce vibrant hues and enhance the glass’s luminosity.
As time went on, the techniques for manufacturing uranium glass evolved. Early artisans relied on simple methods, using traditional tools like blowpipes to shape the hot molten glass. They experimented with different compositions, refining their skills to create more intricate designs. This blend of art and science allowed them to perfect their craft.
In the 20th century, uranium glass gained further popularity, especially in the 1930s. It was mass-produced and marketed as decorative items and tableware. The manufacturing process became more sophisticated, with advancements in furnace technology and molding techniques. However, the use of uranium in glassmaking eventually faced scrutiny due to health concerns.
Today, there’s a revival of interest in hand-blowing uranium glass. Artisans are returning to traditional methods, focusing on the artistry of glassmaking. They carefully manipulate the glowing material, embedding uranium oxide to create unique pieces. This combination of old-world craftsmanship and modern techniques showcases the beauty and complexity of uranium glass, turning production into a form of artistic expression.
The history of uranium glass reflects the development of manufacturing techniques over time. From humble beginnings to a resurgence in craftsmanship, this glass continues to fascinate collectors and artists alike.
Artisanship and Precision
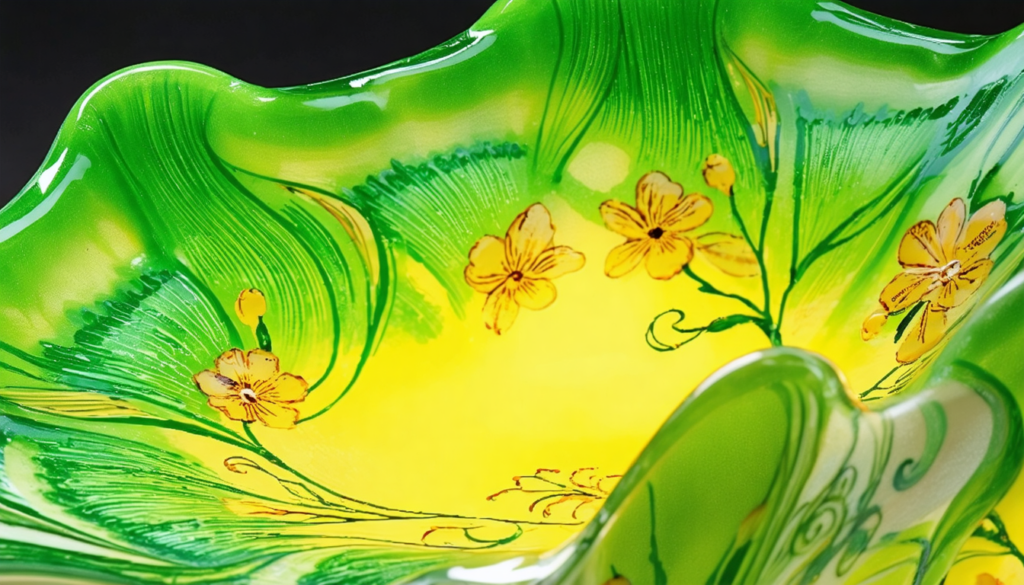
Uranium glass, also known as Vaseline glass, has a fascinating history. It dates back to the 1830s when glassmakers began to add uranium to their glass mixtures. This addition gave the glass a striking greenish hue and made it glow under ultraviolet light.
Over the years, glassmaking techniques evolved. In the early days, artisans hand-blowed glass, requiring a high level of skill and attention. They controlled the temperature carefully, ensuring that the uranium glass took shape perfectly. This method allowed for unique designs that you couldn’t find in mass-produced items.
As manufacturing techniques advanced, factories began producing uranium glass on a larger scale. They used molds and automated processes to create uniform pieces. While this approach increased production, it often sacrificed the artistry and individuality seen in handcrafted items.
Today, there’s a resurgence of interest in traditional glassmaking methods. Many contemporary artisans combine old-world techniques with modern innovations. They create stunning pieces that pay homage to the past while embracing new possibilities. Collectors appreciate these unique works for their vibrant colors and historical significance.
The revival of uranium glass highlights the importance of craftsmanship in manufacturing. It shows that even in an age of automation, the human element in art can create something truly special. This dedication to quality and detail continues to set artisanal glass apart from mass-produced goods.
Techniques and Tools
Uranium glass has a rich history that reflects the evolution of manufacturing techniques. The revival of handcrafted artistry has led to renewed interest in traditional methods. Hand-blowing is one of those techniques that has gained popularity in modern uranium glassmaking.
Artisans use specialized blowpipes to shape molten glass into unique pieces. This process requires skill and years of practice. Controlling the temperature and viscosity of the molten glass is crucial. It allows artisans to create intricate forms and achieve the right thickness.
Many contemporary artisans blend hand-blowing with other methods. They might use molds or add decorative elements. This combination results in striking visual effects and enhances the functionality of the glass.
New workshops are emerging, offering training programs for aspiring artisans. These initiatives aim to foster the next generation of glassmakers. They play a vital role in preserving this extraordinary craft and its techniques for future generations.
Intricate Hand-Painting and Decorative Techniques
Uranium glass has a fascinating history that dates back to the early 19th century. Artisans have long used uranium oxide to create a vivid green or yellow hue in glassware. This unique glass is also known as vaseline glass due to its oily appearance.
The manufacturing techniques for uranium glass have evolved significantly. Early glassmakers relied on simple methods to blend uranium with other materials. As technology advanced, so did the processes. New techniques allowed for intricate designs and patterns to be added to the glass. This transformation showcased not just the glass’s color but also its luminescence.
When artisans paint delicate designs on uranium glass, they demonstrate remarkable skill and patience. Each brush stroke contributes to a vibrant, one-of-a-kind piece. The process often includes kiln-firing, which helps set the colors and adds depth to the artwork.
Gold leaf is another stunning addition. When applied, it enhances the glass’s natural glow. This combination of traditional craftsmanship and modern artistic flair results in extraordinary creations that stand out in any collection.
Collectors appreciate these pieces not just for their beauty but also for their connection to a rich history. Each item tells a story of skilled artisans and their dedication to their craft, making uranium glass a cherished collectible.
Detailed Brushwork Designs
Uranium glass has a fascinating history rooted in innovative manufacturing techniques. The use of uranium in glass dates back to the early 19th century. Artisans discovered that adding uranium oxide to glass produced a vibrant green hue and made it glow under ultraviolet light. This unique property captured the imagination of both manufacturers and consumers.
During the Victorian era, glassmaking underwent significant changes. Factories began to replace traditional hand-blowing methods with machine production. This shift allowed for greater consistency in glass shapes and designs.
Yet, skilled artisans continued to hand-paint intricate designs on uranium glass, preserving the art of craftsmanship. Their techniques meshed modern manufacturing with classic artistry.
Today, enthusiasts appreciate the rarity of uranium glass. Collectors seek out pieces that showcase unique patterns and designs. Each item reflects the skill and creativity of the artist.
The blend of modern methods and traditional techniques makes uranium glass a sought-after treasure. Collectors value these pieces not only for their beauty but also for the story behind their creation.
Gold Leaf Embellishments
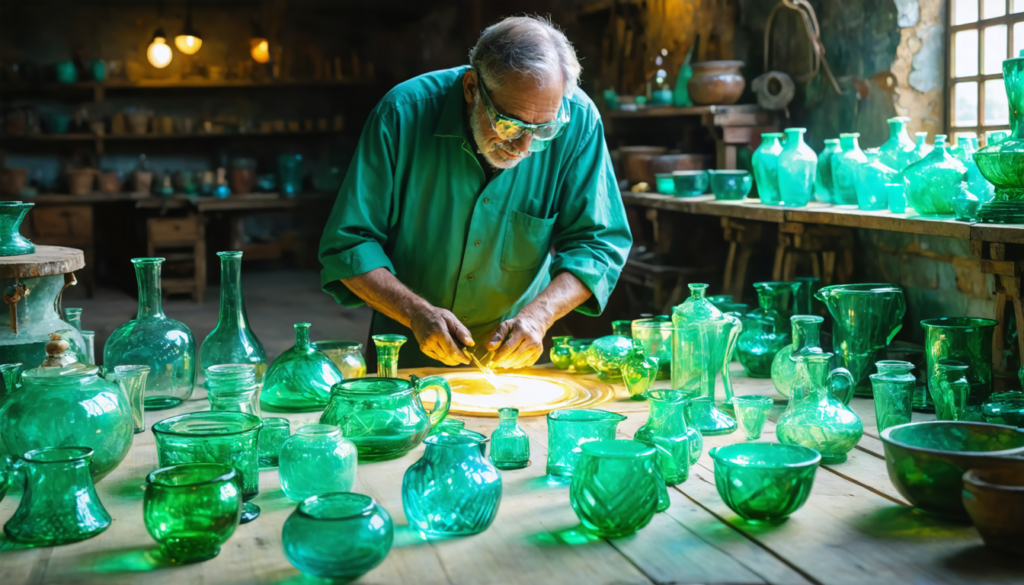
Uranium glass has a fascinating history tied to the development of manufacturing techniques. One notable decorative method is the use of gold leaf embellishments. This technique involves applying thin sheets of gold onto uranium glass, which makes the glass look more beautiful and valuable.
Artisans use detailed brushwork to paint intricate designs, often inspired by styles from the Victorian era. By layering gold leaf and using different colors of glass, artists create stunning contrasts. These contrasts enhance the glass’s glow, especially under UV light.
The gold leaf not only adds visual appeal but also strengthens the glass, acting as a protective layer against wear and tarnishing.
Today, many glassmakers are returning to this traditional technique. This revival draws in collectors who value the skill involved and the historical significance of these handcrafted uranium glass pieces.
The artistry and prestige of owning such items continue to resonate with enthusiasts around the world.
Fluorescence: The Timeless Appeal of Uranium Glass
Uranium glass has a rich history that dates back to the late 19th century. Its unique fluorescence has captured the attention of many collectors and artists. When exposed to UV light, this glass glows with a vivid neon green, adding to its charm. This stunning effect comes from the uranium dioxide mixed into the glass. When light hits the glass, it excites electrons, which then release energy as visible light.
The manufacturing techniques for uranium glass evolved significantly over the years. In the early days, craftsmen used basic methods to create these colorful pieces. As the 20th century progressed, advancements in glassmaking technology allowed for more precise control over the uranium content. This led to a wider range of colors and intensities in the glass. Higher uranium levels produced bright fluorescent shades, while lower levels resulted in the softer yellow-green color known as Vaseline glass.
Advancements in glassmaking technology allowed precise uranium control, creating vibrant fluorescent shades and softer Vaseline glass hues admired by collectors and artists alike.
For collectors, uranium glass represents more than just a decorative item. It stands as a mark of sophistication and class. The glow that emerges under black light draws attention and admiration, making it a sought-after piece in any collection.
The beauty and science behind uranium glass continue to intrigue enthusiasts even today.
Contemporary Artisans Embracing Traditional Methods
Uranium glass has a rich history that dates back to the 1830s. Artisans started using uranium oxide in glassmaking to create vibrant colors and striking designs. Initially, it was popular in the Victorian era, where its unique properties made it a favorite among collectors. The glass glows brightly under UV light, which adds to its allure.
In the late 19th and early 20th centuries, manufacturers began to perfect their techniques. They used vintage molds and crafted pieces through methods like hand-blowing and hand-etching. These techniques required skill and precision, resulting in beautiful, detailed glasswork. Companies like Fenton and Mosser emerged, known for their quality and craftsmanship.
Today, some contemporary artisans are rediscovering these traditional methods. They blend historical practices with modern aesthetics. By incorporating uranium dioxide back into their glass mixtures, they produce eye-catching pieces that resonate with collectors. The fluorescent glow under UV light connects the past with present design trends.
These artisans focus on safety and sustainability while creating their works. They’re inspired by vintage patterns but also strive to innovate. This revival of uranium glassmaking captures the essence of nostalgia, appealing to those who appreciate both history and contemporary artistry.
Collectors are drawn to these unique pieces, which embody a fusion of tradition and modern creativity.
Collectors’ Influence on Artisanal Uranium Glass Production
Collectors play a crucial role in the revival of artisanal uranium glass production. Their interest drives the demand for pieces that reflect historical styles. Many modern glassmakers are returning to traditional techniques, such as hand-blowing and molding. They create unique items that boast vibrant colors and intricate patterns reminiscent of past designs.
This community of passionate collectors is growing. Their tastes influence what artisans produce. Limited runs of items often cater to specific requests. Online platforms and social media connect collectors with artisans, leading to personalized collaborations. This interaction helps both sides create custom uranium glass pieces that resonate with the collectors’ desires.
Specialized exhibitions and events bring collectors and artisans together. These gatherings foster knowledge exchange and celebrate the craft of uranium glass artistry. The shared dedication of this community helps keep the art alive, ensuring that both history and creativity thrive in the world of uranium glass.
Sustainability and Safety in Modern Uranium Glass Manufacturing
Uranium glass, known for its distinctive green or yellow hues, has a rich history that dates back to the 1830s. Early glassmakers used uranium oxide to create vibrant colors and unique effects. Over time, the popularity of uranium glass surged, especially during the Art Deco period of the 1920s and 1930s.
Today, glassmakers focus on improving manufacturing techniques while ensuring safety and sustainability. Many modern artisans use recycled materials in their glass production. This approach not only conserves resources but also reduces waste.
Energy-efficient methods are now common, which help lessen the environmental footprint of making uranium glass. Safety is a top priority. Regulations limit uranium content, often to just 1-2% by weight. This restriction helps minimize radiation risks for both workers and consumers.
Manufacturers rigorously test their products and monitor uranium levels closely to meet the high standards set by the Environmental Protection Agency (EPA) and the Nuclear Regulatory Commission (NRC). Innovations in glassmaking technology allow for greater precision in controlling uranium oxide concentrations.
This means that glassmakers can create stunning pieces that are both beautiful and safe. At the same time, educational programs are raising awareness about the historical significance and contemporary relevance of uranium glass. These efforts empower both creators and consumers to appreciate the art form responsibly.
Frequently Asked Questions
Why Is Uranium Glass Illegal?
Uranium glass, also known as Vaseline glass, has a fascinating history. It’s not illegal, but there are important restrictions. These restrictions stem from concerns about uranium’s toxicity and radiation. This has shaped how people view uranium glass over time.
In the early 20th century, manufacturers developed new techniques to create vibrant, glowing glass using uranium. The glass became popular for its unique appearance, often used in decorative items and tableware. However, as scientific research revealed the health risks of uranium exposure, public perception shifted.
Regulations began to emerge. Manufacturers had to follow strict guidelines to ensure safety. This affected how uranium glass was produced. Despite the risks, many collectors still seek it out today. The market reflects a blend of historical significance and curiosity about its properties.
Environmental impact also plays a role in the conversation. As people became more aware of sustainability, the glass’s legacy was scrutinized. The combination of history, manufacturing techniques, and health implications continues to influence discussions around uranium glass.
Do They Still Make Uranium Glass Today?
Uranium glass has a rich history that dates back to the early 19th century. It was first made in the 1830s when glassmakers discovered that adding uranium to glass yielded a striking green or yellow color. This unique glass quickly gained popularity, especially during the Victorian era when it was often used for decorative items and tableware.
In recent years, interest in uranium glass has surged. Modern glassmakers have embraced the art of crafting this vintage glass, using techniques that blend traditional methods with contemporary innovation. They ensure that the production complies with safety regulations, making it safe for collectors and enthusiasts alike.
Today, uranium glass is created with a focus on eco-friendly practices. The vibrant colors of this glass make it a favorite among collectors, as each piece can vary beautifully in hue. This revival illustrates how history can merge with modern craftsmanship, creating a unique product that honors its past while appealing to today’s market.
When Did Uranium Glass Become Popular?
Uranium glass has an interesting history. It became especially popular during the Art Deco and mid-century design eras. At that time, decorative glassware made with radioactive materials filled antique shops and captivated collectors.
Manufacturing techniques played a crucial role in this rise. Glassmakers discovered how to incorporate small amounts of uranium into their glass mixtures. This added a unique glow under ultraviolet light, making the glassware visually striking. The vibrant colors and patterns appealed to many buyers.
As demand grew, more companies began producing uranium glass. The manufacturing processes improved, allowing for more intricate designs. This led to an explosion of creativity in glass art during the period.
Collectors sought out these pieces for their novelty and beauty. Many people enjoyed displaying them in their homes. Today, uranium glass is still cherished by enthusiasts, who appreciate its historical significance and unique characteristics.
Why Did They Stop Making Uranium Glass?
Uranium glass, known for its vibrant green and yellow hues, became popular in the early 20th century. However, its production faced a significant decline due to growing safety concerns. As awareness of the potential health risks associated with uranium exposure increased, stricter regulations came into play. These regulations made it harder for manufacturers to source materials safely.
Artisan craftsmanship in glassmaking began to pivot. Many artisans shifted away from uranium glass to focus on safer materials. This change reflected a broader trend in manufacturing techniques, as the industry prioritized the health of both workers and consumers. As a result, the market for uranium glass diminished, except among collectors. These collectors still value vintage pieces for their unique color variations and historical significance.
Today, uranium glass is often seen as a relic of the past. Its decline illustrates how safety and health considerations can reshape industries. The legacy of uranium glass remains, appreciated by enthusiasts who cherish its distinct beauty and the craftsmanship behind it.
Conclusion
I found uranium glass by chance in a charming antique shop. Its bright fluorescence caught my eye. This glass has a rich history that goes back to the early 19th century when it was first made. It was popular for its unique glow and color. Over the years, artisans developed various manufacturing techniques that made uranium glass special.
Today, there is a renewed interest in these traditional methods. Craftspeople are bringing back hand-blowing and delicate painting. They focus on safe practices to create beautiful pieces without harming anyone. This approach not only keeps the art alive but also emphasizes sustainability.
The vibrant glow of uranium glass symbolizes a shared journey. It’s about beauty and responsible creation. By preserving these methods, we can ensure that uranium glass continues to be cherished by future generations. Makers and collectors alike will appreciate the artistry and history behind each piece.