The Shift From Handcrafted to Machine-Made Uranium Glass
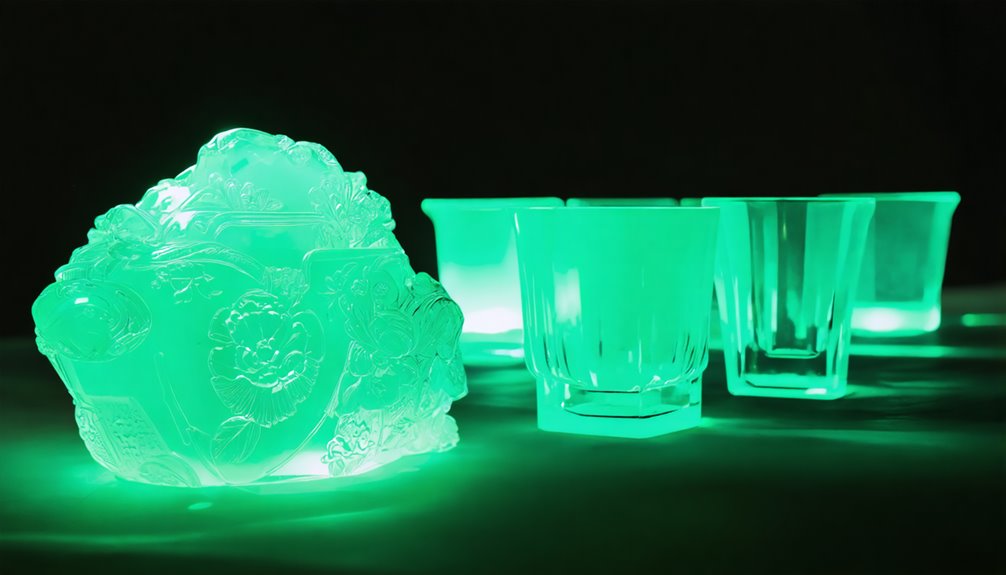
Uranium glass has a fascinating history. It started as handcrafted pieces, each one unique with its own quirks and charm. Craftsmen put great care into making these items, which made them highly sought after. The beauty of these pieces lay in their imperfections, a testament to the artisan’s skill.
Then, in the early 20th century, things began to change. Companies like Fenton and Thomas Webb & Sons introduced machine-made methods. This new technology allowed for faster production and more intricate designs. The shift towards automation meant that glass could be made with precise shapes and patterns, making it consistent and uniform.
While the rise of machine-made uranium glass made it more accessible to the public, it also changed the landscape of collecting. Handcrafted items remained more valuable due to their rarity. However, the mass-produced glass offered a wider variety for collectors to explore. This shift in manufacturing techniques had a lasting impact on the popularity and diversity of uranium glass.
Key Takeaways
The history of uranium glass shows a significant shift from handcrafted methods to machine-made production in the early 20th century. This change allowed for mass production, leading to more uniform designs that appealed to a broader audience.
With machine techniques, manufacturers achieved higher precision. They could create intricate patterns that were often more complex than those made by hand. This variety was a stark contrast to the simpler, more rustic designs of handcrafted pieces.
Industrial manufacturing changed the landscape. It lowered production costs, making uranium glass affordable for many consumers. As a result, more people could enjoy this unique glassware.
Collectors often seek handcrafted uranium glass. They appreciate its individuality and the tiny imperfections that come with human touch. In contrast, machine-made pieces provide consistency and a wide range of styles.
Key companies like Fenton and Thomas Webb & Sons played crucial roles in advancing machine manufacturing. Their innovations not only influenced glass design trends but also shaped the market for collectors. This era marked a pivotal moment in the evolution of uranium glass, blending art with industrial efficiency.
The Artistic Charm of Handcrafted Uranium Glass
Uranium glass has a fascinating history. It dates back to the early 19th century when scientists first discovered the properties of uranium. This glass is notable for its unique glow under ultraviolet light, a result of the uranium content. It became popular in the Victorian era for its striking appearance and was often used to create decorative items.
The manufacturing techniques for uranium glass have evolved significantly over the years. Initially, artisans relied on traditional methods like hand-blowing and molding. These techniques allowed for intricate designs and personal touches. Each piece of uranium glass was unique, showcasing the artisan’s skill.
Early uranium glass artisans used hand-blowing and molding techniques, crafting unique, intricate designs that showcased their exceptional skill and creativity.
As technology advanced, the production of uranium glass shifted. Factories began using machines to create more uniform pieces. This mass production made uranium glass more accessible to the public. However, some collectors still prefer handcrafted pieces due to their individual charm and character.
Today, uranium glass is valued for both its beauty and its historical significance. Collectors often seek out these rare items, sometimes paying high prices at auctions. The blend of artistry and science in uranium glass continues to captivate enthusiasts worldwide.
Revolutionizing Glass Production: Machine-Made Techniques
The move to machine-made uranium glass marked a significant change in the glass industry. With better precision in mass production, manufacturers could create detailed designs with great consistency. This advancement allowed companies like Fenton and Thomas Webb & Sons to meet the growing needs of consumers.
Innovations in glass molding techniques opened up new possibilities for uranium glass products. The market saw an exciting variety of items, appealing to both collectors and everyday buyers.
This transformation not only changed how glass was produced but also influenced the tastes and preferences of consumers, making uranium glass a sought-after choice.
Precision in Mass Production
For centuries, glassmakers created beautiful pieces by hand. This changed in the early 20th century when machine-made uranium glass emerged. This new process gave manufacturers the ability to create glass with a level of accuracy that handcrafting could not match.
With machines, intricate designs and uniform shapes became possible. This not only improved the beauty of the glass but also made it more appealing to buyers. Companies like Fenton and Thomas Webb & Sons took full advantage of these advancements. They increased their production speed and lowered their costs significantly.
Here’s a simple comparison between handcrafted and machine-made glass:
Handcrafted Methods | Machine-Made Techniques |
---|---|
Limited precision | Exact, uniform shaping |
Low production rate | High-speed automation |
Simpler designs | Intricate patterns |
Higher costs | Reduced expenses |
Thanks to automation, uranium glass became very popular. Consumers and collectors found it enchanting. The transition from handcrafting to machine production marked a significant step in the history of glassmaking, showcasing how technology can transform an industry.
Consistency and Replication
As manufacturers began using machine-made methods in uranium glass production, they quickly recognized the importance of consistency and replication. With precise molds and automated machinery, they could effortlessly create detailed shapes and designs. This shift significantly increased production rates and lowered costs.
Machine-made uranium glass featured uniform colors and patterns. Consumers liked this reliability and affordability more than the unique, handcrafted pieces. By the mid-20th century, well-known manufacturers like Fenton and Thomas Webb & Sons embraced these techniques. They met the growing demand in the market while maintaining high quality.
This change in production not only scaled up uranium glass manufacturing but also changed how consumers viewed it. The dependable nature of machine-made items allowed more people to own quality glassware that was once only available to a select few.
Technological Glass Innovations
In the 19th century, glass production changed dramatically. Manufacturers began using advanced industrial techniques, marking a significant shift in how glass was made. Machine-made processes replaced the need for skilled artisans, allowing for mass production of intricate shapes. This change meant that glassmakers could create designs that were once limited to handcrafted methods.
With the introduction of molds and efficient machinery, precision increased. Glass products became more consistent in quality. This improvement made it easier for manufacturers to produce items that were not only beautiful but also reliable. As a result, the appearance of glass became more striking, especially with the use of uranium in the material. Uranium glass, known for its fluorescent properties, added vibrant colors to designs.
The heating and cooling processes used during production also became more controlled. This led to stronger glass that could withstand everyday use while still maintaining its visual appeal.
The transition from limited production to mass production changed the landscape of the glass market. Here’s a quick comparison of the changes:
Before Technological Revolution | After Technological Revolution |
---|---|
Limited production capacity | Mass-production capability |
High costs | Lower costs |
Inconsistent quality | Consistent superior quality |
Fragile designs | Durable, intricate designs |
Exclusive market | Widespread market appeal |
The advancements in manufacturing techniques not only made glass more accessible but also shaped the future of the industry. Glass became a common material in homes and businesses, reflecting the creativity and innovation of its time.
The Impact of Industrialization on Glassware Accessibility
Industrialization changed how glass was made, and this had a big impact on uranium glassware. Before factories started using mass-production methods, uranium glass was carefully made by hand. This made it hard to find and very expensive. Only a few wealthy people could afford to own it.
Then came the Industrial Revolution. Glass factories began to produce uranium glass in large amounts. They could make items that were both high-quality and affordable. By the early 20th century, many factories were creating uranium glass for everyone. They even gave away some pieces as promotions.
The Industrial Revolution transformed uranium glass from rare luxury to affordable beauty, becoming accessible and popular in everyday homes.
This shift meant that the skilled craftsmanship of artisans took a backseat. But it also meant that regular people could buy and enjoy uranium glass. Suddenly, everyday consumers and collectors could access these beautiful, glowing glass items.
This change opened doors and made uranium glass a common treasure in many homes.
Comparing the Aesthetics: Handcrafted vs. Machine-Made Pieces
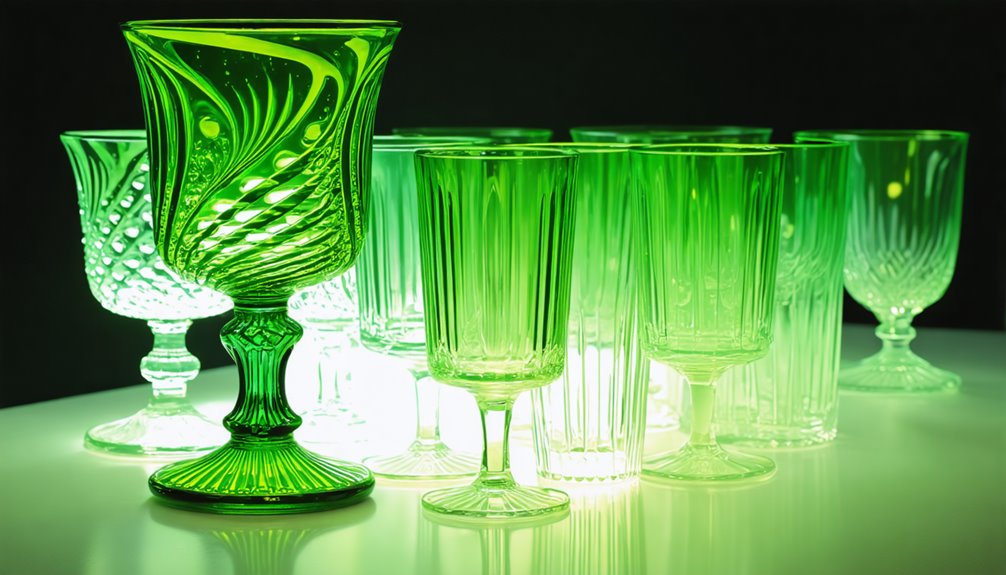
Have you ever thought about how the character of uranium glass varies between handcrafted and machine-made pieces? As a collector, I’ve seen notable differences in these two methods of production, each with its own charm.
Handcrafted uranium glass is unique. It features slight imperfections that highlight the artisan’s skill and personal touch. In contrast, machine-made uranium glass is perfectly uniform. This uniformity can be appealing, but it lacks the individuality found in handcrafted items.
When it comes to artistic details, handcrafted uranium glass shines. It showcases intricate textures and elaborate designs that are often beyond what machines can produce. This craftsmanship adds a layer of beauty that many collectors appreciate.
Fluorescence is another interesting aspect. Both handcrafted and machine-made uranium glass glow under ultraviolet light. However, handcrafted pieces often exhibit richer and more varied fluorescence. This difference can make a handcrafted piece feel more alive and dynamic.
Rarity also plays a role in the appeal of these glass types. Handcrafted pieces typically hold a sense of exclusivity and historical significance. They often come with stories and connections to the artisans who made them.
On the other hand, machine-made uranium glass is more accessible and standardized, which can make it less special to some collectors.
In the end, your preference may reflect whether you value individual craftsmanship or the efficiency of industrial precision. Understanding these differences can enhance your appreciation for the history and development of uranium glass manufacturing techniques.
Cultural Perceptions and Popularity of Uranium Glass Collecting
Uranium glass has a fascinating history tied to its manufacturing techniques. Initially, this glass was handcrafted, making each piece unique. Artisans carefully mixed uranium oxide into the glass, giving it its distinctive glow. As technology advanced, machine-made versions emerged. These pieces maintained the same vibrant color but lacked the individuality of handcrafted ones.
Cultural perceptions significantly shape the allure of uranium glass. Many collectors are drawn to its striking visual appeal. The glass fluoresces under UV light, creating a captivating display. Its slight radioactivity, although minimal, adds an element of intrigue. This combination of beauty and danger attracts enthusiasts.
After uranium restrictions relaxed in the 1950s, production of uranium glass resumed. This revival sparked renewed interest, leading to a vibrant community of collectors. Popular culture also plays a role in this trend. References in films and television highlight uranium glass as a quirky collectible. The thrill of finding these pieces at flea markets enhances their charm.
Collectors appreciate uranium glass for its rarity and historical significance. Each piece tells a story of its time, showcasing the evolution of manufacturing techniques. The unique aesthetics of uranium glass make it a powerful statement piece. It appeals to those who value both beauty and history in their collections.
Safety Concerns and Misconceptions Surrounding Radioactive Glassware
Uranium glass, also known as Vaseline glass, has a rich history that dates back to the 1830s. Initially, glassmakers used uranium oxide to create vibrant green and yellow hues. This practice grew in popularity through the Victorian era, when decorative glassware became a trendy choice for homes.
Manufacturing techniques evolved over the years. Early glassmakers relied on simple methods to incorporate uranium into their glass. As technology advanced, they developed more sophisticated techniques that allowed for the creation of intricate designs and patterns. By the early 20th century, uranium glass was mass-produced and widely available.
Despite its beauty, many collectors worry about the safety of owning uranium glass. It’s important to know that the radiation emitted from these items is minimal. Studies show that the levels are usually safe for brief handling. Authorities such as the United States Environmental Protection Agency (EPA) and the Finnish Radiation and Nuclear Safety Authority emphasize that the primary concern is chemical leaching, particularly when using the glass for food storage.
Many enthusiasts use Geiger counters to measure radiation levels. While some pieces may register higher than normal background radiation, this doesn’t indicate a significant health risk. Collectors should always handle uranium glass with care.
Understanding the history and development of uranium glass can enhance your appreciation for this unique collectible. By knowing the facts and following safety precautions, you can enjoy the charm of uranium glass without unnecessary fear.
Radiation Levels Explained
Uranium glass, also known as Vaseline glass, has a fascinating history in glassmaking. This unique glass contains small amounts of uranium, which gives it a distinctive greenish hue and allows it to fluoresce under UV light. The manufacturing techniques for creating uranium glass have evolved over time, making it a notable part of glass art and design.
Initially, uranium glass was produced in the 1830s. Artisans discovered that adding uranium to glass resulted in vibrant colors and improved clarity. The glass became popular during the Victorian era and was often used for decorative items. Craftsmen used various methods to shape and mold the glass, including blowing, pressing, and cutting.
During the 20th century, uranium glass saw a resurgence in popularity, especially in the 1930s and 1940s. Manufacturers began to mass-produce items like dishes, vases, and other decorative pieces. The techniques became more refined, allowing for intricate designs and patterns.
Today, collectors appreciate uranium glass for its aesthetic qualities and historical significance. It remains an interesting example of how manufacturing processes can influence artistry and design trends.
Despite concerns about radiation, the levels emitted by uranium glass are low and considered safe for casual handling. Collectors and enthusiasts continue to celebrate its unique beauty without fear.
Handling Precautions Clarified
Uranium glass has a fascinating history tied to its unique manufacturing techniques. This glass, often known for its vibrant green color, became popular in the late 19th and early 20th centuries. The incorporation of uranium into glass production started as a way to enhance color and brilliance. Glassmakers discovered that adding uranium oxide could produce striking hues and a vivid glow under UV light.
The manufacturing methods evolved over time. Initially, uranium glass was made using traditional glass-melting techniques. Craftsmen would mix silica, soda, and uranium oxide to create the desired glass. As technology advanced, so did the processes involved. Factories began using automated systems, improving efficiency and consistency in production.
During the 1940s and 1950s, uranium glass reached its peak popularity. The whimsical designs and bright colors attracted collectors. Many pieces were created for household use, from dishes to decorative items. However, as knowledge about radiation grew, concerns about the safety of uranium glass emerged.
Today, collectors appreciate uranium glass for its historical significance and aesthetic appeal. While it remains a subject of curiosity, understanding its production and handling is essential.
Collectors should know that these items can be safely displayed. Enjoying the beauty of uranium glass can be done responsibly, with awareness of its history and properties.
Common Myths Debunked
Uranium glass has a fascinating history that traces back to the 19th century. Many people might think that its radioactive content makes it dangerous, but that’s not true. Let’s explore some truths about uranium glass and its manufacturing techniques.
First, the amount of radiation emitted by uranium glass is very low. In fact, it often produces less radiation than what we encounter from everyday sources, like cosmic rays or certain foods. This means that owning or handling uranium glass is generally safe.
Second, experts from the Finnish Radiation and Nuclear Safety Authority have stated that using decorative uranium glassware poses little to no risk during casual handling. So, if you have a piece on display, there’s no need for concern.
However, it’s important to note that while the glass is safe for decoration, it’s not recommended for food storage. Professionals advise against placing food directly in uranium glass to avoid any potential issues.
As for manufacturing techniques, modern glassmakers have adapted their methods. Today’s uranium glass typically contains less than 1.5% uranium. This is a significant reduction compared to older pieces, which means much less radiation exposure for collectors and enthusiasts.
The Lasting Influence of the Shift on Modern Glass Collectibles
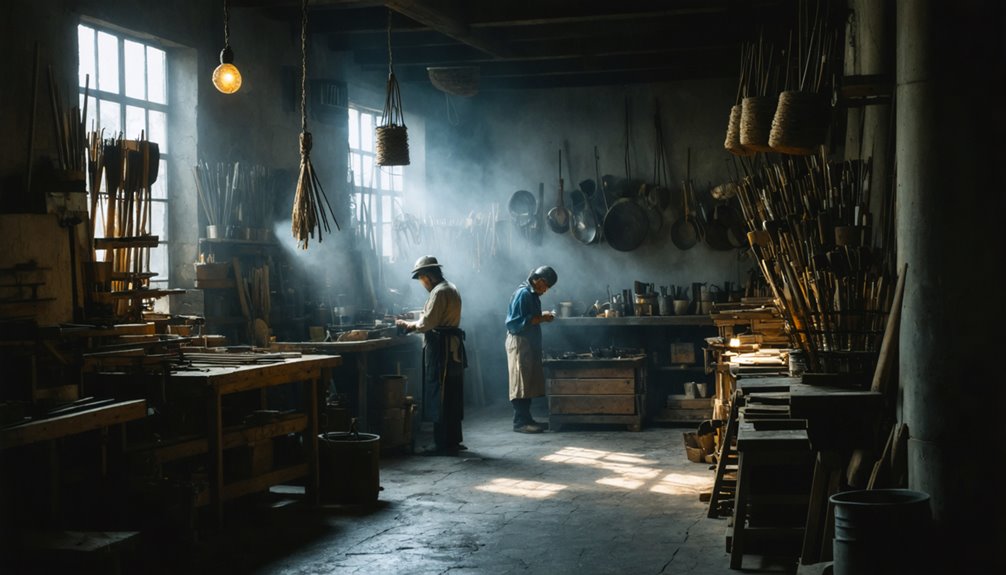
When manufacturers transitioned from handcrafted methods to machine-made uranium glass in the early 20th century, they fundamentally changed modern glass collecting. This shift made production faster and allowed for a wide range of affordable pieces. Collectors could find many options with consistent designs. Renowned brands like Fenton and Thomas Webb & Sons took advantage of new mold techniques. They crafted detailed patterns that made uranium glass more attractive and collectible.
Today, certain machine-made uranium glass items are still highly sought after, showing the lasting influence of industrial production. On the other hand, handcrafted pieces hold their own charm. They symbolize exclusivity, skill, and rarity, which keeps their value strong.
Aspect | Impact on Collectibility |
---|---|
Increased Production Capacity | More options for collectors |
Advanced Mold Techniques | Unique, eye-catching designs |
Affordability | Larger community of collectors |
Frequently Asked Questions
How Did They Make Uranium Glass?
Uranium glass, also known as Vaseline glass, has an interesting history. The process of making it began in the early 19th century. Glassmakers experimented with uranium compounds to create unique colors and effects. These compounds, like uranyl nitrate, were added to molten glass.
The result was a beautiful, greenish-yellow glass that glows under UV light. This glow comes from the tiny amounts of uranium in the glass. It was popular in the Victorian era for its eye-catching appearance.
Over time, glassmakers developed specific techniques to control the glass’s color and fluorescence. They learned how to mix different materials to achieve the desired outcomes. The craftsmanship involved was impressive. Each piece of uranium glass became a work of art, showcasing the skill of the glassmaker.
Today, uranium glass is collected for its historical value and unique properties. Many people appreciate its beauty and the story behind its creation. The techniques used to make uranium glass have influenced modern glassmaking, showing how innovation can lead to lasting traditions.
How to Tell if Uranium Glass Is Vintage?
To figure out if uranium glass is vintage, I look for specific features. First, I check for unique patterns that make each piece distinct. Many well-known manufacturers left identifying markings, which can help confirm authenticity.
Next, I observe the glass under UV light. Vintage uranium glass has a remarkable glow due to the uranium content. This glow is a good sign of its age.
I also look for subtle wear. Over time, genuine vintage pieces develop slight scratches or signs of use. These details can give me confidence that it’s an authentic piece from a past era.
The history of uranium glass is fascinating. It became popular in the late 19th century, around the time when glass-making techniques were evolving. Manufacturers experimented with adding uranium to glass to enhance its color and glow. Eventually, this practice became widespread, especially in the United States and Europe.
Understanding these elements helps me appreciate the craftsmanship and history behind uranium glass. Recognizing these characteristics allows collectors to find true vintage treasures.
Why Is Uranium Glass Illegal?
Uranium glass has a fascinating history. It dates back to the early 19th century when scientists discovered that adding uranium to glass created a unique color and glow. This process became popular in the 1920s and 1930s, especially in America and Europe. Manufacturers loved the vibrant green and yellow hues it produced.
Craftsmen used innovative techniques to incorporate uranium into glass. They mixed uranium oxide with silica and other materials. This combination resulted in a distinctive product that caught the eye of collectors and enthusiasts. The glass was often used for decorative items, tableware, and even jewelry.
Over time, concerns arose about the safety of uranium glass. Although the levels of radioactivity are generally low, some countries began to regulate its use. They sought to protect consumers from potential risks. Today, while uranium glass is not entirely illegal, it is subject to strict regulations in many regions.
If you’re interested in collecting uranium glass, it’s important to understand the laws in your area. Being informed will help you enjoy this unique piece of history while ensuring your safety.
Is Vintage Uranium Glass Toxic?
Vintage uranium glass, with its striking green glow, has a fascinating history. It gained popularity in the late 19th and early 20th centuries. Manufacturers used uranium to give glass a unique color and enhance its brilliance. This glassware was common in homes, showcasing the advances in glass-making techniques.
While some people worry about the radiation, it’s important to understand how to handle it safely. When displayed as a decorative piece, vintage uranium glass can be enjoyed without fear. However, using it for food or drinks is not recommended. The concern lies in the potential for leaching, which could be harmful.
It’s worth noting that the amount of radiation emitted by uranium glass is relatively low. Studies indicate that the levels are not significant enough to pose a health risk when the glass is used correctly. Many collectors appreciate the artistry and craftsmanship of these pieces, celebrating their historical significance.
Conclusion
The history of uranium glass reflects a fascinating journey in manufacturing techniques. Originally, artisans crafted each piece by hand, infusing their work with personal touches. These handcrafted items often displayed intricate designs and unique qualities. But as technology advanced, the rise of machine-made glass changed everything.
Mass production made uranium glass widely available. Families across the world could now own this vibrant material. Instead of being a rare collectible, it became a common household item. This shift marked a significant moment in both the art of glassmaking and the way people interacted with decorative objects.
Many feared the radioactivity of uranium glass, but scientists have shown that it is safe to use. The glass gained attention not just for its glow but also for its historical importance. It serves as a reminder of how innovation can reshape cultural trends and aesthetic preferences. The development of these manufacturing techniques opened doors, making uranium glass a beloved part of many homes.